For which Applications is the SmartRunner Explorer 3-D Vision Sensor with Time-of-Flight Technology Suitable?
Content of This Article
For which Applications is the SmartRunner Explorer 3-D Vision Sensor with Time-of-Flight Technology Suitable?
After the blog article about the SmartRunner Explorer 3-D with stereo vision technology, we will introduce you to the second high-performance technology for 3-D visions sensors: time-of-flight (ToF) technology. The SmartRunner Explorer 3-D ToF sensor offers many of the same benefits as the stereo vision model. Both models produce raw data that can be used to create a highly accurate 3-D point cloud. Continue reading to learn applications for the 3-D vision sensor with time-of-flight!
The ToF sensor excels in longer range applications as it can detect up to 7.5 meters. It is also a good solution for faster data acquisition with a scan frequency of 30 Hz compared to the 10 Hz of the stereo vision model.
The SmartRunner Explorer 3-D ToF ensures precise detection due to a special four-phase measurement evaluation process. The reflected light is checked at four separate points along the returned wavelength to reduce noise and increase signal quality. Another advantage of the ToF sensor is that it can be used both indoors and outdoors. Its 940-nm infrared light source makes it insensitive to ambient light. With an image resolution of 640 x 480 pixels and an opening angle of 47° x 35°, the SmartRunner Explorer 3-D ToF can offer a wide detection range while delivering highly accurate measurement data. More details on the detection capabilities can be viewed below:
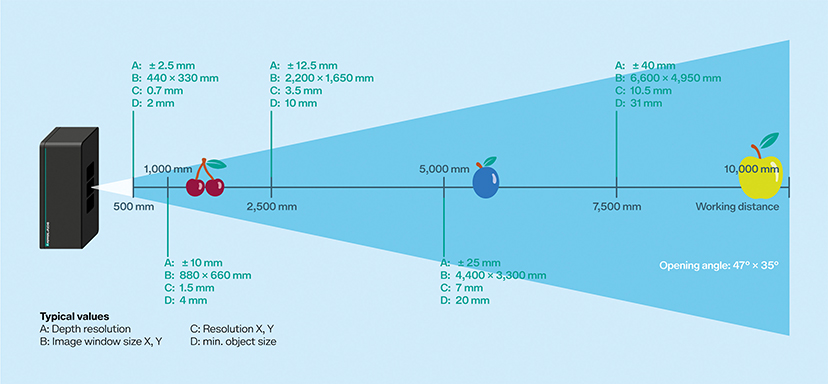
The SmartRunner Explorer 3-D ToF is ideal for applications that require a longer detection range, but not the resolution of less than half a millimeter that can be achieved with stereo vision. Let’s take a look at two application examples that are perfect for time-of-flight technology and this new SmartRunner sensor.
Pallet Pocket Detection
Detection of pallet recesses has been a problem in the material handling world for many years, and a constant problem with automated forklifts and stacker cranes. The SmartRunner Explorer 3-D ToF is an ideal solution to this problem, as it can easily generate an image that clearly identifies the “pallet pocket.” The automated device makes adjustments to ensure the forks are properly aligned to safely lift the pallet load.
The ToF sensor’s faster operating frequency of 30 Hz provides information much quicker. This allows the automated guided vehicles to adjust the forks dynamically without slowing down their operating speed any further.
The 3-D point cloud in the image below was created using the ViSolution demonstration software available from Pepperl+Fuchs. The color pattern indicates the distance from the target to sensor, with blue representing objects furthest from the detection face.
The pallet recesses are easily identifiable in the 3-D images and highlighted by the red boxes.
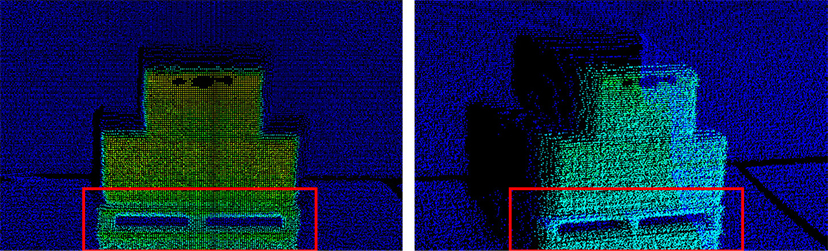
Tire Measurement and Positioning
Measuring and positioning tire length is important information for applications where machines are used to lift and move a vehicle. In many cases, these trolleys clamp the vehicle by the tires. The size and position of the trolley is critical for the proper lifting and moving of such a heavy object. Such trolleys are often used in car repair shops, automated parking garages, or car wash applications. Before the introduction of 3-D vision sensors, it was difficult to find a reliable solution.
When viewing the 3-D point cloud generated by the SmartRunner Explorer 3-D ToF, it is easy to identify the wheel well and tire of this model car by eye. However, the 3-D sensor also provides detailed measurement data on multiple axes that can be used to calculate the length of the tire and its position within the evaluation window. The longer range and large detection area of the ToF sensor make it the ideal choice for this application. The ability to be used both indoors and outdoors provides flexibility for this type of application, as the environmental conditions for moving vehicles can vary greatly.
Again, the colors indicate the distance of the target from the sensor face, with blue representing the objects furthest away. The tires and wheel wells are highlighted in the red boxes.
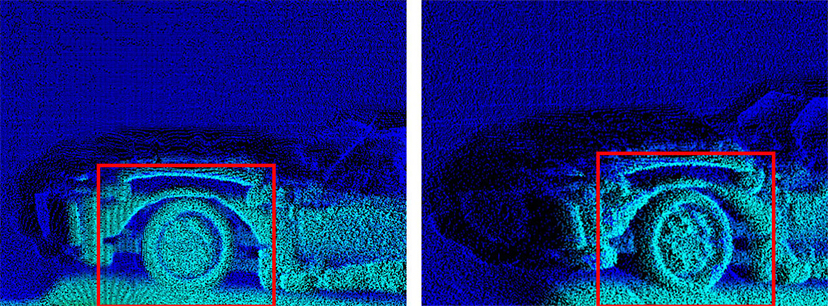
Similar to our previous discussion of the SmartRunner Explorer 3-D stereo vision, this is only a small sampling of the potential applications that time-of-flight technology offers. As a raw data device, there are endless uses and applications that can be solved by 3-D data acquisition.
Please contact Pepperl+Fuchs Tech Support to discuss applications for the 3-D vision sensor with time-of-flight!
More Information
This blog article is part of a series of articles about vision sensors in use. You may also be interested in:
- For which Applications is the SmartRunner Explorer 3-D Vision Sensor with Stereo Vision Technology Suitable?
- Vision Sensors—Three Examples for Industrial Vision in the Automotive Industry (Part 1)
- Vision Sensors—Three Examples for Industrial Vision in Material Handling (Part 2)
- Vision Sensors—Use Cases for Industrial Vision in Material Handling (Part 3)
- Vision Sensors—Use Cases for Industrial Vision in the Automotive Industry (Part 4)
Subscribe to our newsletter and receive regular news and interesting facts from the world of automation.