For which Applications is the SmartRunner Explorer 3-D Vision Sensor with Stereo Vision Technology Suitable?
Content of This Article
For which Applications is the SmartRunner Explorer 3-D Vision Sensor with Stereo Vision Technology Suitable?
With the SmartRunner Explorer 3-D, Pepperl+Fuchs offers a highly innovative product that uses stereo vision technology. This raw data sensor converts objects and environments into a highly accurate 3-D point cloud. The 3-D measurement data is processed directly in the sensor and made available immediately via fast Ethernet TCP/IP, without the need for external calculations.
With a detection range of approximately 1 meter, the SmartRunner Explorer 3-D with stereo vision technology can perform very high precision detection over a relatively large area. This data is provided at a rate of 10 times per second or at a maximum pass rate of 1 meter per second. By using a two powerful 1.4 mega pixel cameras, this sensor can achieve a resolution of less than 0.5 millimeters at full range!
The main technical advantage is that the sensor has a pattern lighting. This is useful for fast depth measurement and for depth measurement of homogeneous surfaces.
Now this is a lot of information on the specifications of the SmartRunner Explorer 3-D, but the more important question is how can this technology be used in an actual application? The stereo vision version of the SmartRunner Explorer 3-D is best suited for applications that have a short detection range but require maximum precision. Let’s take a look at two application examples for stereo vision technology:
Quality Control—Part Presence Detection
In the following example, the SmartRunner Explorer 3-D with stereo vision technology is used to verify whether an object has been properly placed in the shipping box. The two images we compare show the box with the object correctly placed in the foam insert, while the other image shows it is missing entirely.
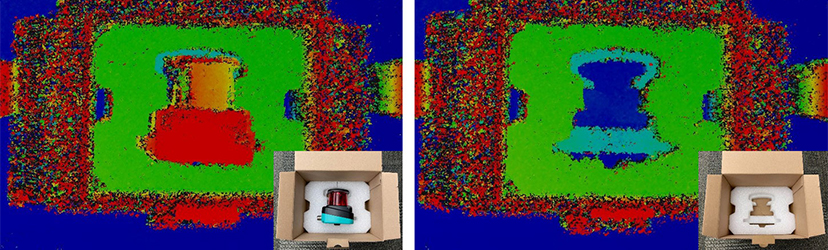
Blue colors represent objects that are further away, while red indicates objects that are closer to the sensor face.
The 3-D point cloud in the images was created using the ViSolution demonstration software, and the colored patterns indicate the distance between the sensor and objects in the field. Blue colors represent objects that are further away, while red indicates objects that are closer to the sensor face.
If you look at the 3-D image, you can quickly see that the part on the image to your right is not in the package. The advantage of 3-D vision in this application over 2-D sensors is that now you get a full view of the product instead of only a section. So if the position of the box changes, you can still track the placement of the part inside the box. In parallel, the SmartRunner Explorer 3-D provides a 2-D image from the right and/or the left camera.
Inspection—Completeness Check
In this second example, the SmartRunner Explorer 3-D is in use to ensure that the transparent bottle process is properly filling the packages to maximum capacity. In this application, the first box is filled with six transparent bottles, and the second box is missing one bottle, indicated by the blue area in the image. Blue again indicates objects that are further away from the sensor.
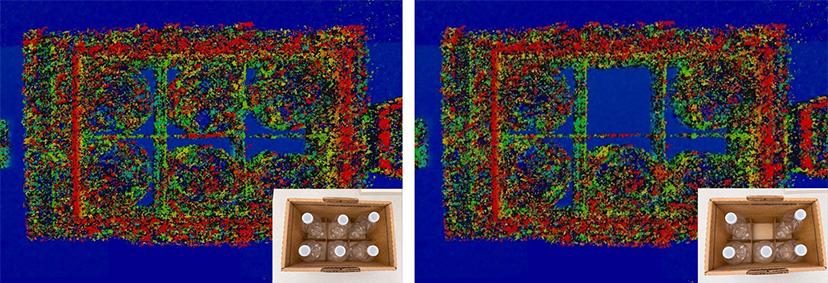
The SmartRunnner Explorer 3-D uses a projected image above the target where the camera captures an image, so transparent objects can now be fully detected.
Transparent objects are generally very difficult to detect with camera-based vision sensors. However, the SmartRunnner Explorer 3-D uses a projected image above the target where the camera captures an image, so transparent objects can now be fully detected. Traditional camera-based detection relies on target contrast to evaluate the image.
As in the first application example, you can quickly see the difference between the two images and determine that a bottle is missing from the package. The measurement data generated also indicates this to your control system to ensure that the boxes are fully loaded before they are sent on to shipping. Again, 3-D vision offers a distinct advantage, as you can monitor both rows of bottles with a single sensor, whereas a 2-D solution would require multiple devices.
There are infinite possibilities for a raw data device because it gives you the flexibility to capture the measurement data and use it for any need or application. With these two application examples, we hope to inspire creativity for possible uses of stereo vision technology. Look out for more information about the SmartRunner Explorer 3-D.
Subscribe to our newsletter and receive regular news and interesting facts from the world of automation.