Precise Position Detection with the PXV Absolute Positioning System
Content of This Article
Precise Position Detection with the PXV Absolute Positioning System
Whether electric monorail systems, crane trolleys or stacker cranes—they all have to be positioned very precisely over long distances in the plant. With 0.2 mm resolution over distances of up to 100 km, PXV technology perfectly meets the demands of exact absolute positioning, even over long and complex distances. In this blog article, we take a look at what makes camera-based linear positioning with the PXV system so unique and how the combination of the 2-D camera system with the Data Matrix code tape ensures precise position detection and maximum process reliability.
How Does the PXV Absolute Positioning System Work?
The PXV positioning system consists of a 2-D read head equipped with modern camera technology and the Data Matrix code tape. The read head moves parallel to the code tape in X direction and supplies highly accurate position data every 10 or 25 milliseconds, such as the X absolute position, the Y offset to the center of the code tape, the traversing speed and quality values of the code tape, which can be read out with the control/PLC. With the aid of the integrated illumination unit, the reading head—which is extremely immune to ambient light—detects the position marks even under difficult conditions. The marks are printed as two-dimensional Data Matrix codes on the self-adhesive code tape. As soon as just one of five codes is detected in the reading window, precise position detection is possible. Gaps in the code band of up to 75 mm can also be bypassed. In this way, the 2-D camera system combined with the multiple redundant Data Matrix code tape ensures maximum process reliability.
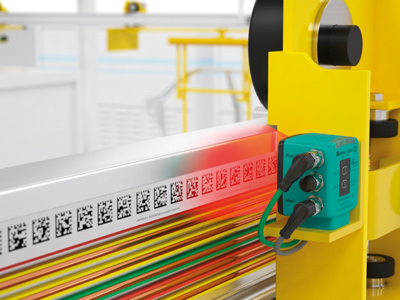
The PXV system consists of a 2-D read head and a Data Matrix code tape.
Simple Installation and Commissioning
The system is easy to install and at the same time operates completely maintenance-free, contactless and without moving parts, so that only low follow-up costs are incurred. For example, the PXV can be quickly and easily put into operation by mounting the read head at a nominal distance of 100 mm from the code tape. Immediately after switching on, the sensor supplies the required data via RS485, SSI or the fieldbus interfaces PROFINET, or EtherNet/IP. In addition, parameterization of the inputs and outputs for signaling NoPos/events or the mounting direction of the read head to the code tape is possible via Data Matrix control codes, via the PC, or directly via the controller.
Flexible and Complex Track Layouts
The self-adhesive Data Matrix code tape enables exact absolute positioning even in particularly extensive systems and over all track layouts. Tailored to the application, it can be supplied individually for track lengths from 1 m to 100 km and applied flexibly. In addition to a very high inclination tolerance of +/- 30° to the code tape, the PXV also has a high depth of field of 50 mm, so that the system provides reliable data at all times, even for complex track layouts such as tight curves, strong inclines and declines, circular shapes, or hollow shafts.
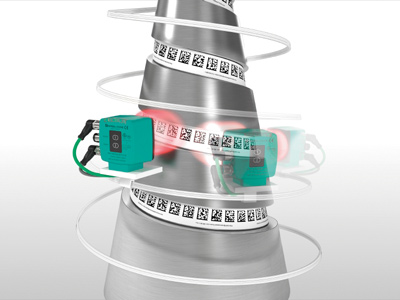
Precise linear positioning even for complex track layouts.
Code Redundancy Ensures Reliable Processes
Due to the particularly large reading window of 120 x 80 mm, the read head reads up to five Data Matrix codes in just one operation and is insensitive to contamination or damage to the code tapes. The code redundancy allows contamination or interruptions of the code tape up to 75 mm as well as a large Y-tolerance to the read head—without affecting the performance.
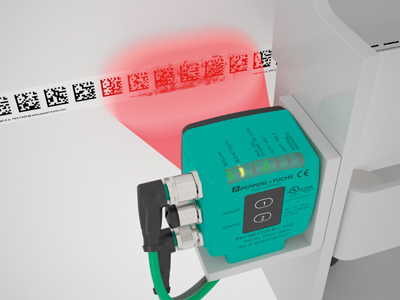
Heavily contaminated and damaged codes are read reliably due to code redundancy.
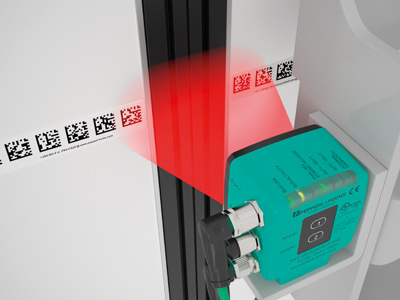
The PXV read head tolerates code tape interruptions of up to 75 mm.
The additional data output of the code tape quality and the number of codes read within one measurement allow continuous monitoring of the code tape and detection of contamination on the read head. The constant output allows users to plan and carry out preventive and early cleaning measures for the code tape.
Would you like to learn more about camera-based linear positioning?
More Information
Subscribe to our newsletter and receive regular news and interesting facts from the world of automation.