4 Sensor Applications to Control a Metal Coil Feeding Line
Content of This Article
4 Sensor Applications to Control a Metal Coil Feeding Line
Coiled sheet metal is automatically unrolled and fed into a stamping press for forming. To ensure a consistent quality of the end product, the feed rate, sheet alignment, and material advancement must be precisely controlled. The goals are to minimize planned and unplanned machine downtime while maximizing part quality and yield. Pepperl+Fuchs offers various sensors that ensure smooth and efficient coil feed processes. Get to know four sensor applications how to efficiently control a metal coil feeding line.
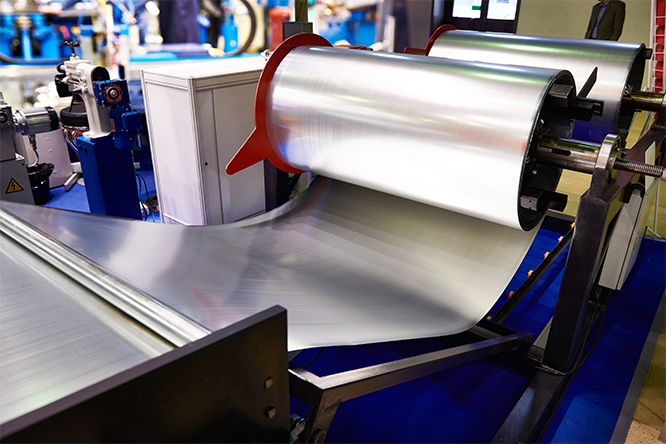
Monitor Decoiler for Diameter Feedback
It is crucial for every plant operator to keep production processes as efficient as possible. So it is important to avoid waiting times for personnel, whether until a coil has been completely decoiled, or production is even halted because a new coil is not available in time. Using analog sensors to automatically signal for a fresh coil at the ideal replacement point optimizes changeover times.
Both analog ultrasonic and laser-based photoelectric sensors are equally capable of providing continuous coil diameter feedback. In most applications, these sensor principles are interchangeable. However, both offer unique features that provide advantages dependent on the environment.
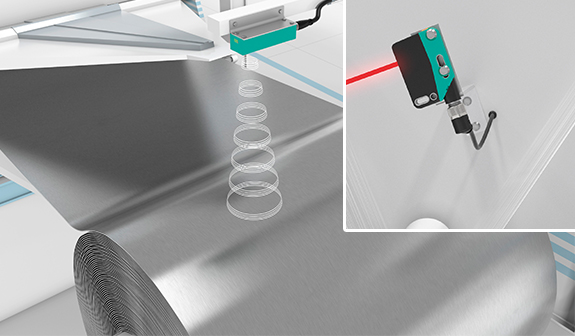
Both ultrasonic and laser analog sensors provide high resolution coil diameter feedback.
The strength of ultrasonic technology lies in its reliable operation in changes in the target gloss or color as well as in the presence of contaminants such as oils. This makes ultrasonic sensors ideal for this application.
When the sensing environment is relatively clean, laser-based sensors such as the VDM28 also provide analog feedback, with the added benefit of a narrow sensing beam. This gives them a slight advantage in detecting very narrow sheet metal, or in tight spaces where surrounding obstructions might interfere with the wider ultrasonic beam. The visible light spot of the laser also allows for quick and easy alignment.
Detect Sag Loop to Adjust Feed Rate
As the sheet approaches the press, a sag loop is formed. The loop control adjusts the feed rate based upon the sag height. If the material sag is too small, a servo driver is triggered to pull more, while a high loop requires slowing down.
In the “pre-sensor” days, this feedback was often provided by a dancer arm. But these mechanical elements loosen, break, stick, and wear out. Mounting a noncontact ultrasonic sensor such as the UC2000 analog model or laser sensor such as the VDM28 above the center of the sag loop is the most modern solution for loop feedback. Both offer sensing ranges that allow loop detection from several feet above the ground. Mounting from above also prevents falling particles from obstructing the sensor’s view. As with decoiler sensor solutions, the decision between sound- and optic-based sensor technologies depends on the prevailing environmental conditions and preferred setup (calibration).
Verify Sheet Presence and Alignment
Before the sheet enters the press, it is customary to verify that it is present and properly aligned. A standard thru-beam photoelectric sensor such as the OBE25M-R200 ensures that the metal sheet has reached the cutting area of the press. However, it is also useful to verify that the sheet is not misaligned or faulty. Photoelectric slot sensors are suitable for this task.
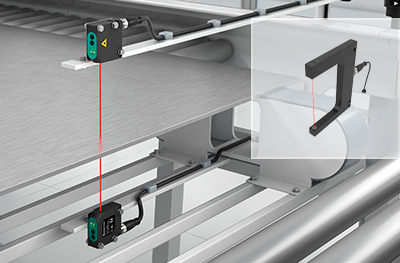
Photoelectric thru-beam sensors detect sheet presence, photoelectric slot sensors can detect the correct alignment.
Control Part Cut Length
As the uncoiled sheet passes through rolls, the part cut length can be precisely controlled with two sensor principles. First, an incremental rotary encoder like the model ENI58IL provides measurement values to the control system. In parallel, an inductive sensor detects pilot holes in the metal sheet. If a hole is detected, a signal is sent to the controller to add up the increments, which initiates the cut.

A fed sheet spins a rubberized conveyor roller. The rotary encoder’s measurement pulses determine the cut length.
More Information
Subscribe to our newsletter and receive regular news and interesting facts from the world of automation.