Vision Sensors—Three Examples for Industrial Vision in the Automotive Industry (Part 1)
Content of This Article
Vision Sensors—Three Examples for Industrial Vision in the Automotive Industry (Part 1)
It is hard to imagine the automotive industry without industrial vision. Whether for automatic component inspection, code reading on vehicle components, or the positioning of electric monorail systems—the application areas of vision sensors are as diverse as the portfolio of industrial vision. Learn more about three application examples of vision sensors in the automotive industry in this blog article.
1. Automatic Component Inspection in Car Body Manufacturing with the SmartRunner Matcher
In car body production in the automotive industry, components are welded together in robot welding cells. For this purpose, prefabricated sheets are manually placed in the robot arm. During insertion, a defective sheet can get caught in the gripper. To ensure that the sheet is complete before the subsequent process, certain contour features must be detected—and without delay. For this task, a laser profile sensor from the SmartRunner Matcher series is attached to the robot gripper.
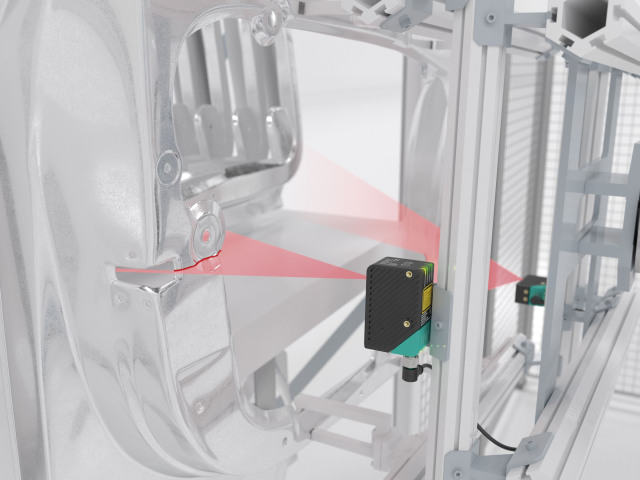
The SmartRunner Matcher is attached to the gripper of the robot and records the height profile of the inserted sheet metal.
The sensor detects the contour of the sheet and compares it with the previously taught height profile. In doing so, it directly passes on deviations so that the subsequent work step is not necessary. The SmartRunner Matcher ensures consistently reliable detection of the components, regardless of object contrast or the influence of ambient light. In addition, the laser profile sensor can be intuitively parameterized and easily integrated into various control systems due to a wide range of connection options.
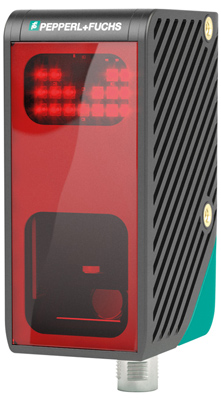
Laser Profile Sensor SmartRunner Matcher
2. Reliable Reading of 1-D, 2-D, and DPM Codes on Vehicle Components with the VOS-I
In automotive production, components are marked with a Data Matrix code to track them specifically during their processing steps and to ensure consistently high quality. Depending on the required robustness, the code is applied to the component as a name plate or as Direct Part Marking (DPM) by laser or needles. Reflective surfaces, dirty or uneven codes, and the rapid movement of components are only some of the challenges that the code readers must overcome. The VOS-I reliably reads all common 1-D and 2-D codes at distance ranges from a few centimeters to two meters—whether in motion on assembly lines or on robot arms.
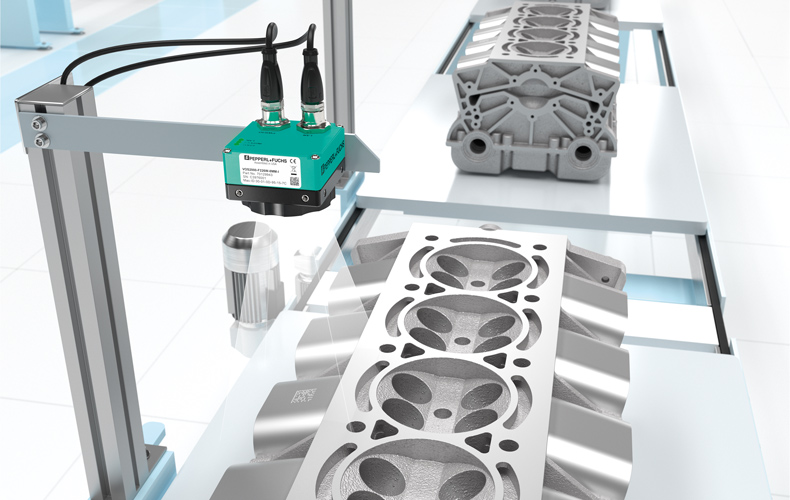
The VOS-I universal code reader provides reliable identification for plant control and ERP systems.
Pepperl+Fuchs offers the matching VOS-I vision sensor for reliable reading of all common 1-D and 2-D codes. The sensor‘s lighting can be optimally adapted to the application. With electronic filters, the VOS-I can, for example, enlarge the code or mask out edge effects such as scratches, therefore improving readability. In addition, all relevant interfaces for data communication are available with I/O, Ethernet TCP/IP, PROFINET, EtherNet/IP, and RS-232. The output string for integration into the ERP system can be adapted with the script without much effort.
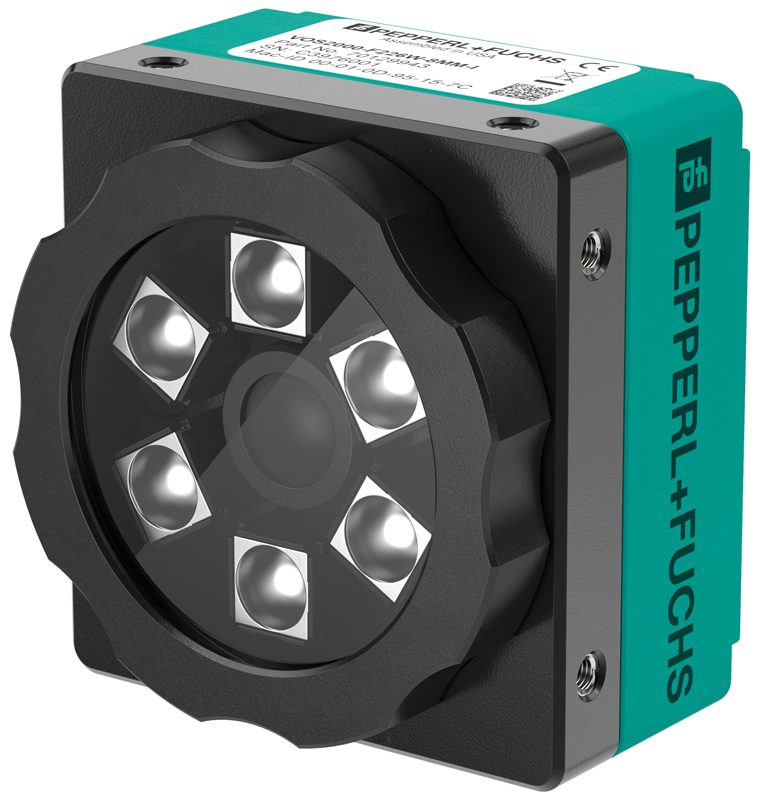
VOS-I Universal Code Reader
3. Reliable Positioning of Monorail Conveyors with the PXV Absolute Positioning System
Monorail conveyors enable the transport of engines, drive trains, vehicle doors, or complete vehicle bodies along the production line. The monorail carriers are equipped with their own sensor system, motor and control system. They travel independently on the rails and reliably transport the parts along all routes, regardless of whether they involve inclines, curves, or switches. To ensure maximum availability and avoid downtimes due to collisions, the carriers must be positioned with high precision over the entire route. With track lengths from up to 100 km, a position resolution of ±0.2 mm and a travel speed of up to 8 m/s, the PXV absolute positioning system offers the optimum solution.
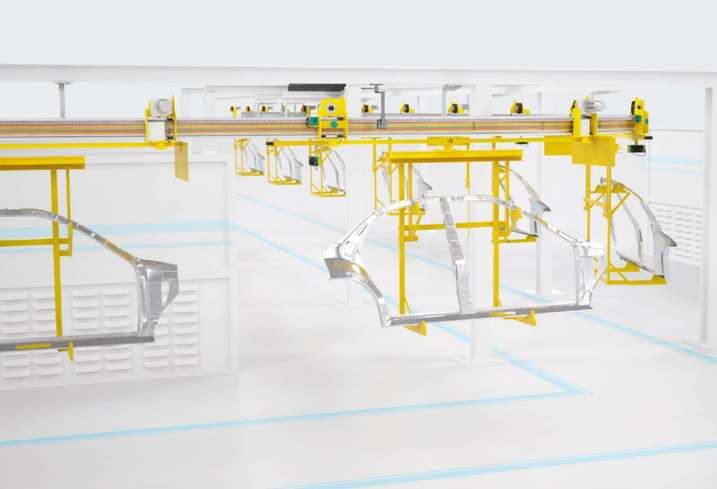
The 2-D read head of the PXV Data Matrix positioning system is installed directly on the vehicle of the electrified monorail system.
The PXV absolute positioning system consists of a Data Matrix code tape attached along the rail and a read head installed directly on the carrier at a distance of 100 mm from the rail. The 2-D camera outputs the current absolute position of the carrier in relation to the Data Matrix code tape to the control system. The PXV not only enables quick and easy commissioning, but also eliminates the need for calibration or maintenance intervals as with other technologies. The safePXV variant with PROFIsafe also offers special protection for man and machine according to SIL 3/PL e with only one sensor.
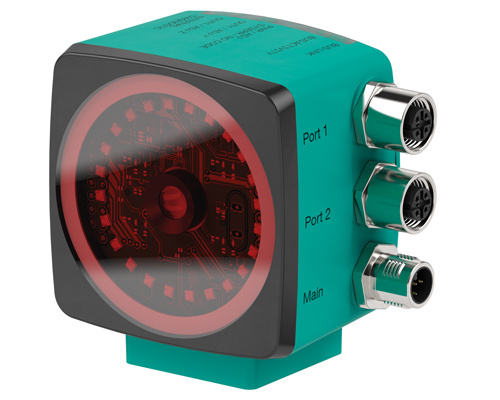
PXV absolute positioning system
Are You Still Looking for a Solution for Your Application?
Pepperl+Fuchs offers a comprehensive portfolio of universally applicable vision sensors, application- or customer-specific products, and turnkey solutions. The powerful technologies can be used to solve a wide variety of tasks in the field of industrial vision. Talk to experts and together we will find the vision product or solution that optimally fits your individual requirements.
Subscribe to our newsletter and receive regular news and interesting facts from the world of automation.