Monitoring Inclination and Acceleration in Dynamic Applications with the Inertial Measurement Unit IMU F99
Content of This Article
Monitoring Inclination and Acceleration in Dynamic Applications with the Inertial Measurement Unit IMU F99
Wherever inclination and acceleration measurements are distorted by external accelerations in dynamic applications, the inertial measurement unit F99 can be a suitable solution. By combining an accelerometer, gyroscope, and intelligent sensor fusion algorithm in one unit, the inertial measurement unit (IMU) compensates for dynamic movements and thereby ensures precise inclination measurement. The IMU F99 is specially designed for outdoor use due to its degree of protection (IP68/IP69K) and can also be used on public roads with its E1 approval, meaning that the industries and applications are diverse. In this blog article, you will discover six application examples for inclination and acceleration monitoring with the inertial measurement unit IMU F99.
Reliable Inclination Monitoring for Onboard Scales
On-board weighing systems are used to calculate the weight of materials on mobile equipment. For example, modern wheel loaders calculate the weight of the loaded material directly in the shovel. A trip to a central weighing location is therefore no longer necessary. To avoid false results due to external accelerations, the inertial measurement unit F99 is used. It provides acceleration-compensated data and ensures accurate weight calculation without loss of time.
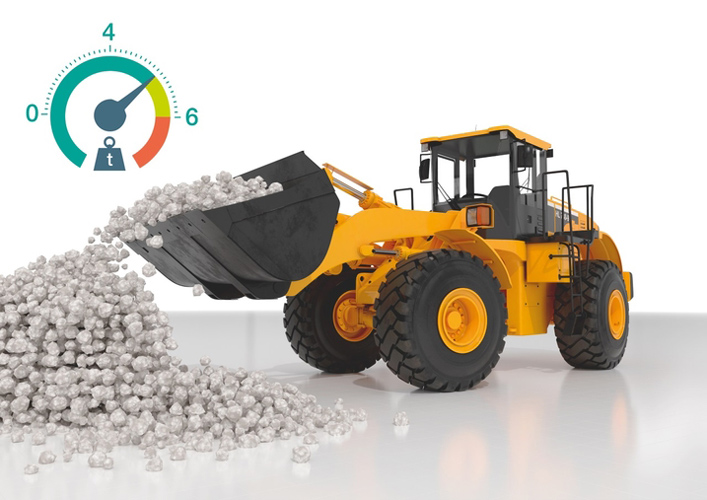
The IMU F99 provides acceleration-compensated data for the on-board weighing system and ensures accurate weight calculation in real time.
Steering-Angle Limit on Large Vehicles
The IMU F99 is ideal for inclination measurement on large vehicles such as wheel loaders, dump trucks, or forklifts to prevent damage to equipment or personnel. If these machines are used on uneven terrain, too much steering angle in an inclined position can cause the vehicle to tip over. To prevent this, the IMU F99 reliably detects the angle of inclination even during external accelerations such as starts or braking, so that the steering angle of the vehicle can be regulated and tipping can be prevented.
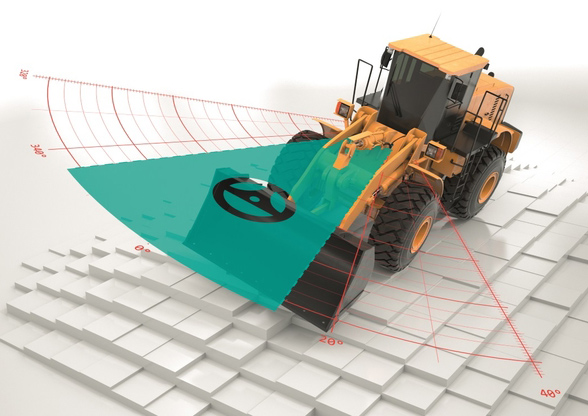
The IMU F99 reliably detects the angle of inclination even during external accelerations such as starts or braking.
Precise Positioning of Excavator Shovels
During excavation work, excavator operators receive both precise information on the excavation, such as external dimensions and depth, and an image of the actual movement of the machine on a display. The operating personnel uses this information to control the shovel. In order to position the shovel precisely, the exact position must always be recorded—even during movement. For this purpose, an IMU F99 is mounted on each of the moving parts of the arm, the shovel, and the chassis. The devices measure acceleration and rotation rate and use them to calculate the dynamic inclination of the moving component. In addition, the position of the shovel tip absolute to the center of the earth is also recorded while the excavator is moving. With the inclusion of external GPS data, this enables global absolute position measurement of the excavator shovel.
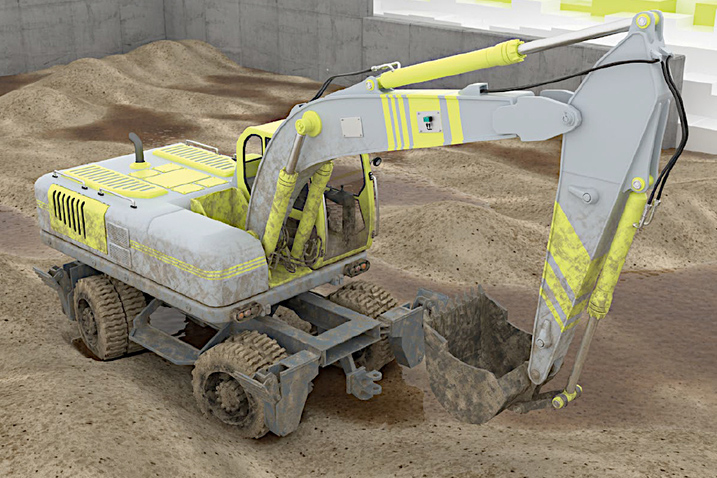
The IMU F99 ensures precise positioning of the excavator shovel by calculating the dynamic inclination of the moving components of the arm, the shovel, and the chassis.
Boom Inclination Control in Agricultural Machinery
In agriculture, machines with long booms are used to apply liquid fertilizers and pesticides. One of the aspects that influences the optimal distribution of these fertilizers and pesticides is the distance between the boom segments and the ground. Ideally, it should always remain the same within a minimum tolerance range. The IMU F99 measures the acceleration and the rotation rate and forwards the calculated dynamic inclination angle of the boom to the control system.
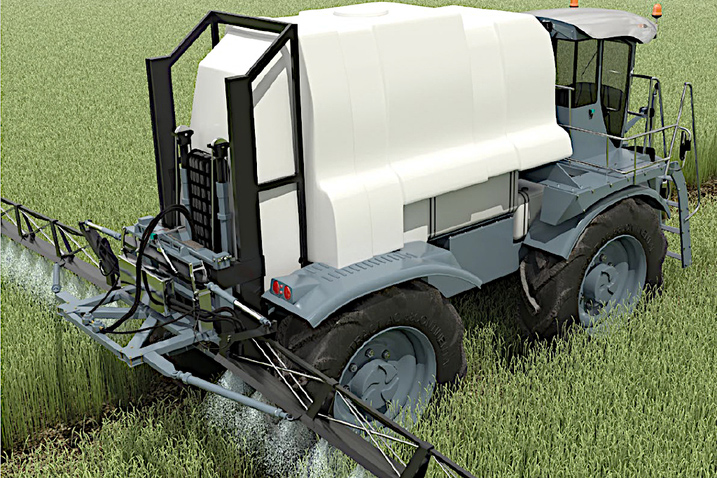
The IMU F99 measures the distance between the boom segments and the ground and ensures that the boom height remains in optimal spraying position.
Reliable Monitoring of Wind Turbines
To ensure safe and efficient operation of wind turbines, various sensors are used to monitor, for example, the tower vibration, the position and rotational speed of the hub, and the torsion and icing of the rotor blades. The inertial measurement unit F99 is capable of performing all these tasks and meets the special requirements for operation in wind turbines. Using the same type of device reduces the effort in asset management, while the IMU F99 reliably monitors the plant components.
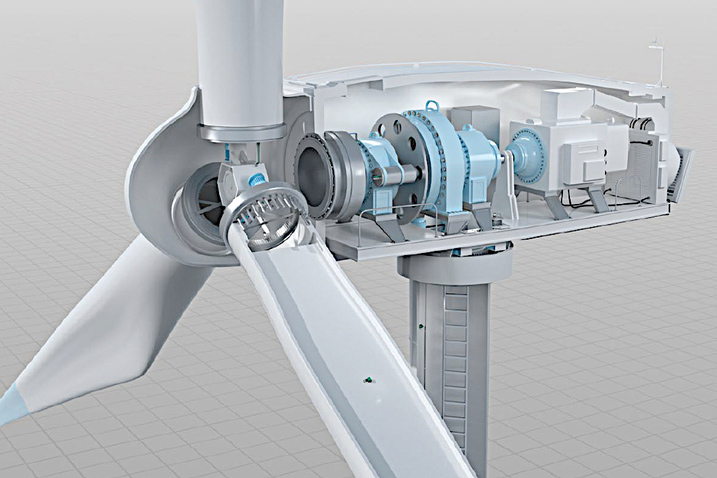
The IMU F99 reliably monitor the plant components of the wind turbine such as tower vibration, the position and rotational speed of the hub, and the torsion and icing of the rotor blades.
Dynamic Position Detection for AGVs
AGVs are increasingly used to transport parts and products between different production stations. Their navigation is usually carried out with the help of optical sensors. However, in order to be able to determine its own position at any time, an AGV requires additional data. The inertial measurement unit F99 provides this data. It records any deviation from straight-ahead travel with high accuracy by measuring the Coriolis force with a capacitive MEMS sensor. In this way, the inertial measurement unit outputs the rotation rate values of the driven curves and enables dynamic position determination and precise navigation of the AGV.
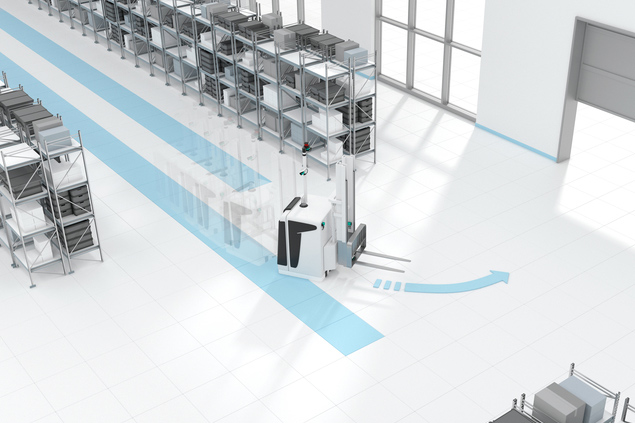
The IMU F99 enables dynamic position determination and precise navigation of the AGV, recording any deviation from straight-ahead travel.
Subscribe to our newsletter and receive regular news and interesting facts from the world of automation.