Vision Sensors—Use Cases for Industrial Vision in Material Handling (Part 3)
Content of This Article
- 1. Precise Automated Guided Vehicle (AGV) Adjustment when Picking up Load Carriers with the PGV Positioning System
- 2. Simple Drill Holes for Perfect Positioning with PHA Vision Technology
- 3. Quality-Assured Removal Control for Packing Stations with the SmartRunner Detector
- Are You Still Looking for a Solution for Your Application?
- More Information
Vision Sensors—Use Cases for Industrial Vision in Material Handling (Part 3)
Whether it is the adjustment of automated-guided vehicles, the positioning of stack carriers, or the removal control during order picking processes—material handling faces a multitude of challenges. To meet these, Pepperl+Fuchs offers a broad portfolio of vision sensors in material handling. Learn more about three application examples from storage and material handling in this blog article and discover the solution for your industrial vision task.
1. Precise Automated Guided Vehicle (AGV) Adjustment when Picking up Load Carriers with the PGV Positioning System
AGVs or so-called bots are frequently used in warehouse logistics to transport load carriers such as gear rack systems or trolleys. To do this, the bots first drive into a recess under the load carrier, lift it, and then continue to the specified destination.
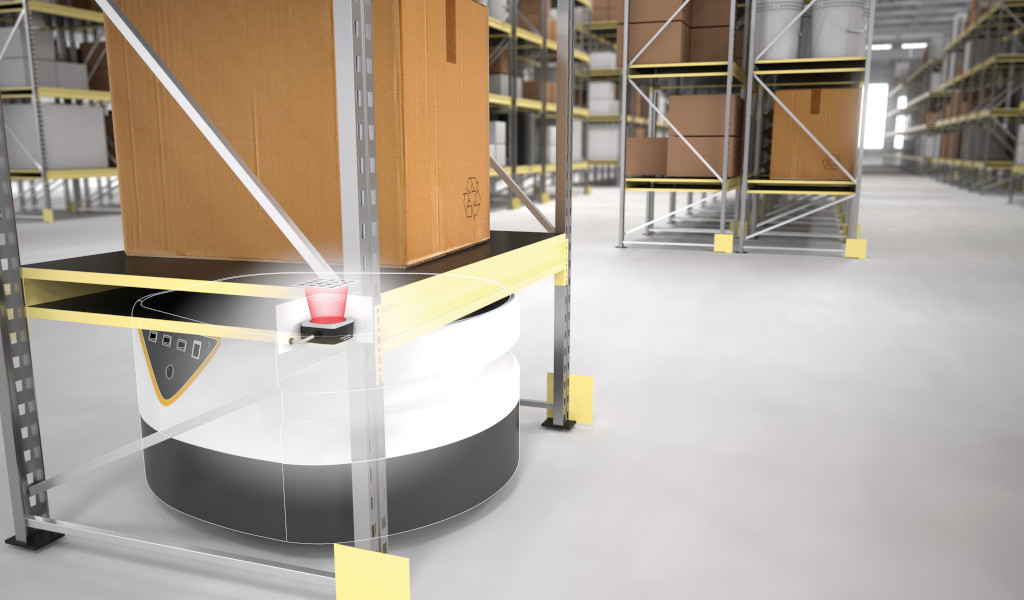
The position guided vision (PGV) positioning system reliably identifies the load carrier and simultaneously ensures high-resolution position determination. The PGV uses Data Matrix tags with several codes attached to the underside of the container. These are detected without contact by the read head, which consists of a camera system with integrated lighting unit and large reading window. At the same time, the orientation of the read head to the tag and therefore the exact position of the target object is determined. Accordingly, the control system can use the data from the PGV to bring the bot into the correct position directly during feed-in. This ensures that the load carrier is picked up correctly.
PGV positioning system
The incident light method with internal illumination unit ensures tag detection even under difficult lighting conditions. The PGV is easy to integrate both due to the compact design of the read head and the open protocol on the software side. It also allows simple commissioning via plug-and-play.
2. Simple Drill Holes for Perfect Positioning with PHA Vision Technology
Positioning stacker cranes in front of the correct compartment in automated high-bay warehouses is a challenge because the steel frameworks are subject to varying degrees of fluctuation. In order to approach the storage compartment precisely, a two-step procedure consisting of rough and gear rack fine positioning is often used. In the first step, the storage compartment is only approached roughly at high speed. In the second step, the compartment is fine-positioned down to the millimeter range using reference objects.
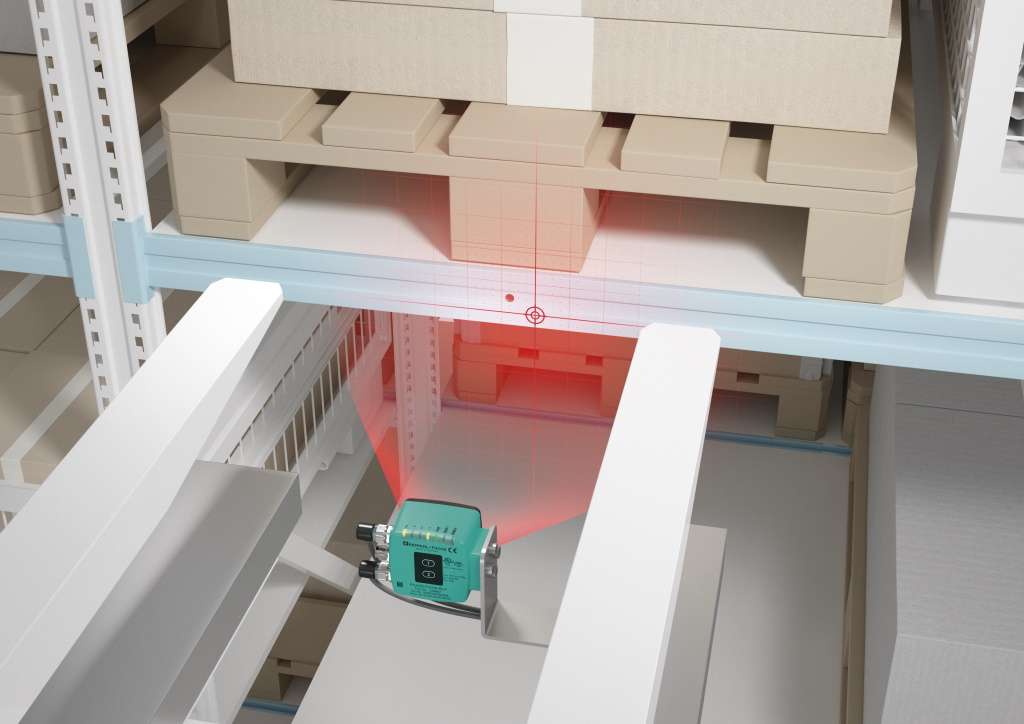
PHA vision technology uses a simple and efficient method. Only one drill hole in the steel profile of the bearing frame is required as a reference point, saving costs for installation, maintenance, etc. of traditional reference objects. For rough positioning, the target only needs to approach to the point where the reference hole falls within the sensor’s detection range of up to 120 × 150 mm. Once the PHA detects the hole, it calculates the deviations between the actual and target positions for the X and Y axes. Therefore users do not have to install a separate detection device for each coordinate direction.
PHA vision technology
The PHA has either four switching outputs for direction information as well as an Ethernet TCP/IP interface or a PROFINET interface. All necessary system components such as camera, infrared illumination, evaluation and interfaces are combined in one compact device.
3. Quality-Assured Removal Control for Packing Stations with the SmartRunner Detector
At packing and picking stations, transport boxes of different heights are conveyed to the removal station via a conveyor belt or roller conveyor. At the removal station, the conveyor line bends at a 90-degree angle. The employees have to reach into the correct box and remove the corresponding product. The gripping process is detected directly above the box so that unnoticed reaching through outside the sensor’s detection range is ruled out.
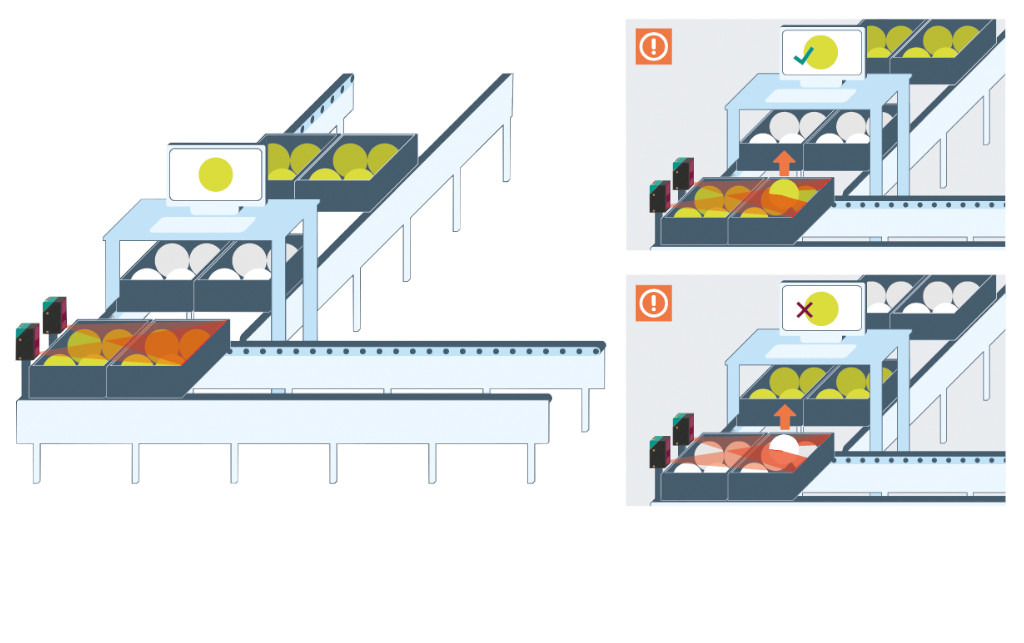
The SmartRunner Detector laser profile sensor offers a suitable solution for monitoring only one side of the station. It combines transmitter and receiver in a single device and is insensitive to reflective objects. In addition, the detection range can be limited to the opening of the box and a minimum height of the objects to be detected can be parameterized. Therefore, neither handles next to the box nor smaller foreign objects trigger a signal.
SmartRunner Detector laser profile sensor
The SmartRunner Detector combines powerful laser light section technology with a vision sensor and LED lighting. Employees always pick the product indicated by a light spot (pick by light). The pick in the detection area can be read out as a 2-D image via the RS-485 interface and is therefore used for quality assurance and documentation.
Are You Still Looking for a Solution for Your Application?
Pepperl+Fuchs offers a comprehensive portfolio of universally applicable vision sensors, application- or customer-specific products, and turnkey solutions. The powerful technologies can be used to solve a wide variety of tasks in the field of industrial vision. Talk to experts and together we will find the vision product or solution that optimally fits your individual requirements.
Subscribe to our newsletter and receive regular news and interesting facts from the world of automation.