How to Reliably Monitor Valves on Hydrogen Pipes
Content of This Article
How to Reliably Monitor Valves on Hydrogen Pipes
Hydrogen is increasingly being used as an alternative to fossil fuels in industry and, as with conventional natural gas, it is transported via pipes and pipelines. Not least due to the explosion hazard posed by hydrogen, safety and reliability must always be ensured along the entire transport route. One critical area of concern is the valves on the pipes. A valve that is incorrectly open or closed can have fatal consequences. To prevent this, Pepperl+Fuchs offers a whole range of solutions for reliable monitoring and feedback on the valve positions on hydrogen transport pipes. But which solution is best for which application? Find out about the different product solutions how to reliably monitor valves on hydrogen pipes, whether indoors, outdoors, or in hazardous areas.
Valve Position Monitoring in Harsh Industrial Environments and Hazardous Areas
Dual inductive sensors are based on a simple sensing principle with two sensors in one housing. This sensor design is mounted directly on a valve actuator and houses two perfectly placed inductive sensing elements that monitor the position of the valve, rather than using one sensor to detect when the valve is open and one when it is closed. As the valve opens or closes, one of the inductive sensing elements is always triggered, ensuring reliable processes.
Since hydrogen transport pipes are generally located outdoors in large industrial plants, the especially rugged F31K2 dual inductive sensors for valve position feedback are ideally suited for this purpose. The “house-in-housing” design of the sensors—made of glass-fiber reinforced plastic and coated aluminum—provides double mechanical protection and maximum impermeability to withstand any weather or adverse ambient conditions. Temperatures ranging from -40 °C to +75 °C, salt water, and UV radiation have little effect on the rugged sensors. The versions with approvals up to Zone 2/22 or Zone 0/20 are suitable for use in hazardous areas. The visible, integrated valve position indicator and the translucent housing of the F31K2 dual inductive sensors enable the status of the valve to be checked at any time—even from a distance and in poor visibility.
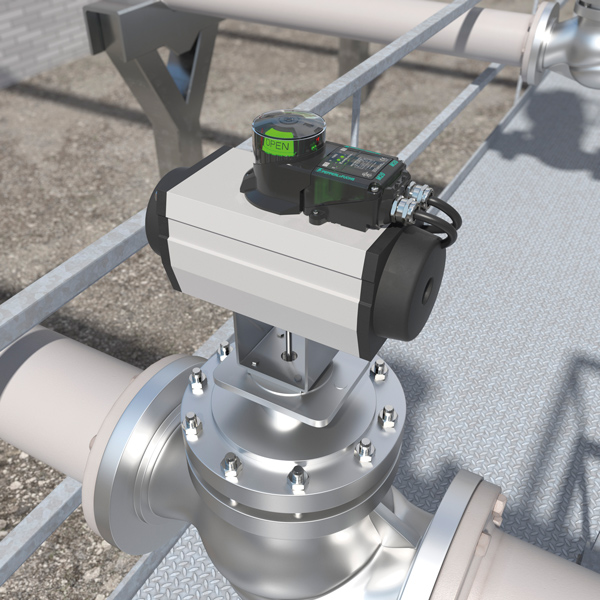
The especially rugged F31K2 dual inductive sensors are ideally suited for valve position feedback in harsh industrial environments and hazardous areas as on hydrogen pipelines.
Precise Recording of Valve Position on Pneumatically Operated Diaphragm Valves and Linear Control Valves
Inductive positioning systems are based on the combination of an inductive sensor and a damping element. The noncontact inductive position measurement systems PMI from the F90 series are easy to install and provide the ideal solution for precise recording of the valve position on pneumatically operated diaphragm valves or linear control valves. No special target is required for noncontact recording—simple steel actuators or even valve components can serve as actuators. This not only saves time and effort, but also makes it an especially flexible and cost-effective solution.
The analog output of the PMI F90 series ensures continuous transmission of the recorded valve position. Users can choose between different adjustable output signals: 4 mA … 20 mA or 0 V DC … 10 V DC. The IO-Link interface also allows the system to be individually adapted to specific applications. The PMI F90 inductive positioning system is available in lengths of 40 mm, 80 mm, and 120 mm, and is available as an ATEX version for safe use in hazardous areas up to Zone 2/22.
The inductive position measurement systems PMI F90 series are the ideal solution for precise recording of the valve position on pneumatically operated diaphragm valves or linear control valves.
A Complete Solution for Valve Control on Hydrogen Pipes
In addition to standard products for monitoring the valve position on hydrogen transport pipes in industry, Pepperl+Fuchs offers a special complete solution for valve control. The combination of a standard inductive sensor and a cable protection system is suitable for use on hydrogen pipes. This type of system allows four individual positions of a control valve to be detected. The cable protection system consists of a particularly durable and flexible conduit that protects the sensor cable from being pinched, nicked, or cut when used in extreme applications. A damaged cable will prevent the transmission of signals from the sensor. Worse, a damaged cable with exposed wiring can cause serious problems in an area with explosive gases.
The especially rugged, stainless steel design and extended temperature range from -40 °C to +100 °C make the solution ideal for use in harsh industrial environments. With approval for hazardous areas up to Zone 2/22, the complete system comprising inductive sensors and a cable protection system is also suitable for hydrogen pipes running through areas in which explosive atmospheres are prevalent. The solution can be individually adapted to common valve types and allows reliable valve control on hydrogen pipes and pipelines.
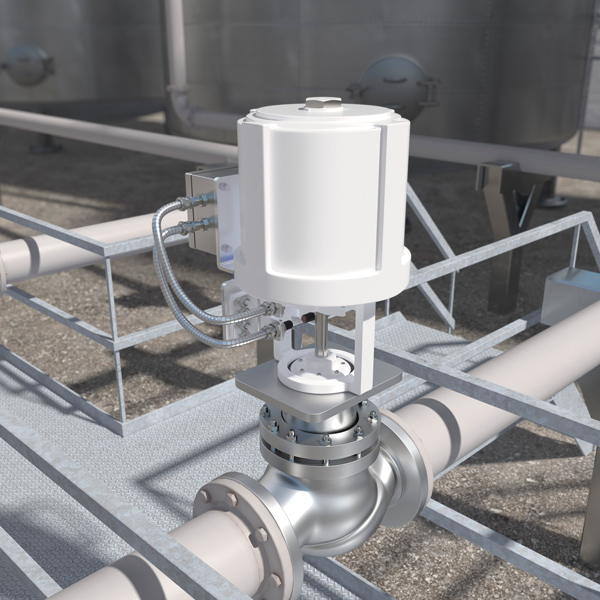
Pepperl+Fuchs offers a special complete solution for valve control, which is a combination of a standard inductive sensor and a cable protection system, suitable for use on hydrogen pipes.
Subscribe to our newsletter and receive regular news and interesting facts from the world of automation.