When Does it Make Sense to Use a Vibration Sensor?
Content of This Article
When Does it Make Sense to Use a Vibration Sensor?
Pepperl+Fuchs recently launched a new portfolio of sensors for vibration monitoring. In this blog article, you will learn more about how vibration sensors work. Learn how you can use these sensors to monitor the condition of your machines and perform predictive maintenance.
The Importance of Condition Monitoring
Condition monitoring is very important to assess the condition of your machine. It helps to avoid unplanned downtime, reduce maintenance costs, increase production levels and provide predictive maintenance.
Condition monitoring uses vibration monitoring because vibration sensors give you the ability to record speed, acceleration, temperature and bearing condition characteristics. The condition of a machine can be read from the changes in these values:
- Vibration velocity RMS (mm/s) can change due to component fatigue, such as alignment errors or imbalance problems.
- The vibration acceleration RMS (g) can be affected by mechanical friction. This may be due to lack of lubrication, bearing wear, or a dragging part on the machine. When measuring vibration acceleration, the RMS value, i.e. the square root of the average value, is calculated to monitor the long-term effects of vibration.
- The temperature output of the vibration sensor has the advantage of detecting abnormal temperatures on the machine, which can be caused by high friction, electrical problems, or insufficient lubrication.
- The bearing condition characteristic value is a calculation of the peak acceleration value divided by the RMS acceleration value. This value can be used to determine bearing wear. It should be noted that after calculating the bearing condition rating, the diagram and ISO standard for the part in question must be analyzed, because an electric motor, for example, has a different bearing condition rating diagram than a centrifugal pump.
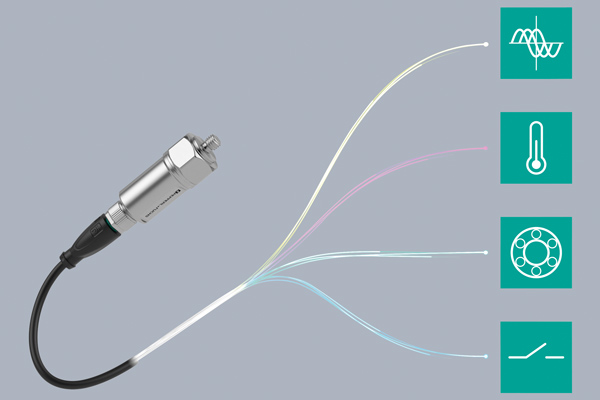
The vibration sensors from Pepperl+Fuchs determine vibration velocity and acceleration as well as temperature and bearing condition.
What Are the Benefits of Vibration Sensors?
Vibration sensors can reduce downtime and maintenance costs by monitoring the condition of your machine over time. This enables predictive maintenance: so you can address potential risks before catastrophic consequences occur for your machine or product. With vibration sensors with IO-Link output, you can monitor the condition of your machine remotely, giving you a round-the-clock view of potential problems.
What Technologies Are Typically Used in Vibration Sensors?
Two of the technologies that can be used in vibration sensors are MEMS and piezo. Pepperl+Fuchs’ vibration sensors are based on MEMS technology: a MEMS (Micro Electro Mechanical System) is placed on the board to measure the gravitational acceleration acting on the micromechanical element. The capacitance between the plates is monitored and then converted into an accurate result. There can be multiple axes, such as an x-axis and a y-axis, with a MEMS system for each axis orientation.
Piezo technology, on the other hand, measures the electrical potential created by applying force to metal plates with quartz crystals between them. Compared to the piezo element, the MEMS has the advantage of being smaller, less expensive and easier to place on the PCB. In addition, the MEMS typically has a frequency response of 1 Hz to 2 kHz. In contrast, the piezoelectric element has a higher frequency response (typically from 5 Hz to 10 kHz). Therefore, it is needed for high frequency measurements. Since many machines only have vibration frequencies between 1 Hz and 1000 Hz, MEMS technology is more common for these applications.
What Are Typical Output Options for Vibration Sensors?
Typically, vibration sensors have an analog output. There is also an IO-Link output option that provides access to acceleration, velocity, temperature and bearing condition characteristics in one sensor. In addition, IO-Link provides the ability to connect an IO-Link master that can take all vibration information and distribute it between PLC, HMI, SCADA, cloud or any of these combinations – enabling Industry 4.0.
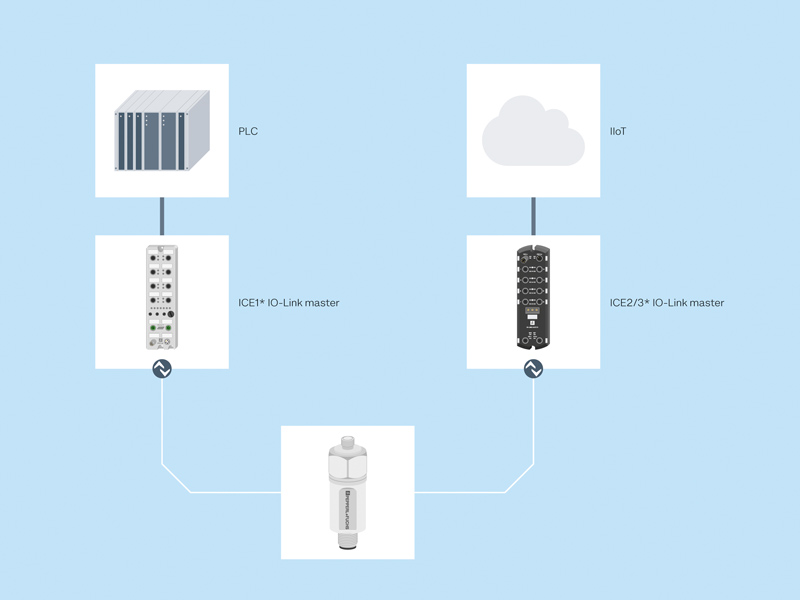
Via an IO-Link master, the measurement data of the vibration sensor can be transmitted to the PLC or used for Industry 4.0 applications.
In What Markets Can Vibration Sensors Be Used?
There are many markets and applications where vibration sensors can be used. Some of the most common industries are warehousing and materials handling, packaging, food and beverage, oil and gas, renewable energy, and mobile equipment. Possible applications include motors, turbines, generators, rotary pumps, fans, conveyors, mills and centrifuges. In any of these applications, Pepperl+Fuchs vibration sensors can be used to reliably and continuously monitor the condition of machinery.
More Information
Subscribe to our newsletter and receive regular news and interesting facts from the world of automation.