Monitoring the Condition of Your Plants With Vibration Sensors
Content of This Article
- The portfolio of vibration sensors
- Vibration sensors vs. acceleration sensors
- Acceleration sensors for the measurement of short-term vibration acceleration
- Vibration sensors for measuring long-term vibration changes
- Vibration and acceleration sensors in wind turbines
- Control of the turbine with the acceleration sensor F99
- Condition monitoring with the VIM vibration sensor
- More Information
Monitoring the Condition of Your Plants With Vibration Sensors
To enable long-term monitoring of vibrations, Pepperl+Fuchs recently launched a new portfolio of vibration sensors. You can find out what distinguishes these products in the following blog article. Using a wind turbine as an application example, we will also show you how you can use vibration and acceleration sensors in combination to keep an eye on both long-term and short-term changes in vibration. Continue reading to learn how to perform condition monitoring using vibration sensors!
The portfolio of vibration sensors
Pepperl+Fuchs has recently started offering a range of vibration sensors to perform reliable measurements of vibration velocity and acceleration in low or high frequency ranges. Compared to similar products, Pepperl+Fuchs’ vibration sensors have approvals up to SIL 2, a large measuring range of up to 128 mm/s, and automatic condition detection for ball bearings. Due to their robust housing and encapsulated electronics, the sensors impress with maintenance-free operation and a particularly long service life.
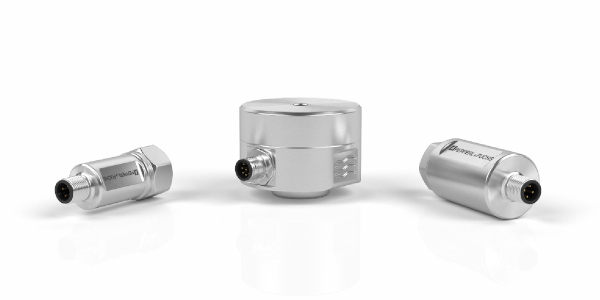
The three designs in the portfolio are available with different certifications and approvals. In this way, you can find the right vibration sensor for every application:
- VIM3 series: The compact VIM3 series is suitable for applications up to SIL 1/PL c, and has output options for analog or IO-Link.
- VIM6 series: The VIM6 series is approved for hazardous areas up to Zone 1/21. With an extended temperature operating range of -40°C … +125 °C, the sensors are ideal for high-temperature areas.
- VIM8 series: Due to a particularly robust housing made of duplex steel, the vibration sensors of the VIM8 series are designed for use in offshore applications as well as in harsh and hazardous areas of Zone 1/21. Moreover, the sensors have an approval up to SIL 2/PL d.
Vibration sensors vs. acceleration sensors
Not only vibration sensors, but also acceleration sensors from Pepperl+Fuchs are used to measure changes in vibration: Both record the vibration acceleration in g. Nevertheless, the sensors differ in their technical operating principle and are therefore each suitable for different applications.
Acceleration sensors for the measurement of short-term vibration acceleration
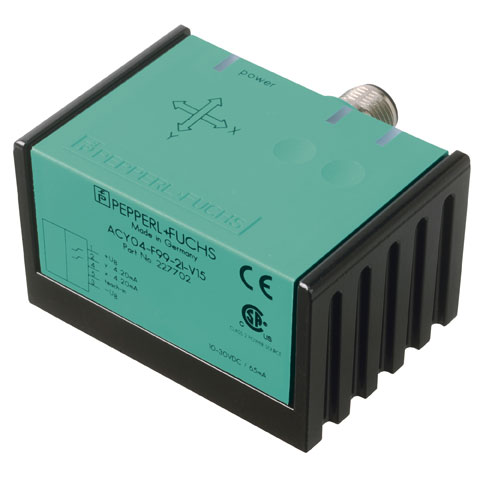
The acceleration sensors of the F99 series are able to measure 0 Hz and therefore accelerations that are in the low-frequency range. The acceleration values that the sensors record are not averaged. Instead, the instantaneous values are output directly as time signals. Therefore, the F99 is suitable for detecting short-time, one-time acceleration events in the millisecond range.
Vibration sensors for measuring long-term vibration changes
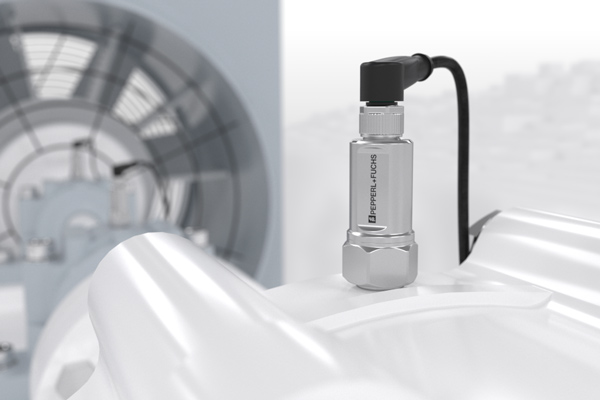
In contrast to the F99 acceleration sensors, the vibration sensors of the VIM series only display a measured value from a frequency of at least 1 Hz. This means that there must be a cyclic movement of the machine at least once per second for the VIM sensor to display a measured value greater than zero. Furthermore, unlike the F99, the VIM sensor does not output instantaneous values, but a pre-filtered RMS value. This is an average value resulting from averaging over a period of up to 12 seconds.
The VIM series sensors should therefore deliberately not react to short-term acceleration events such as those indicated by the F99 acceleration sensor. Otherwise, for example, a forklift passing near the machine would lead to a change in the output data as a short-term acceleration event. This event should be deliberately filtered out and not displayed as an error state of the machine.
Instead, the RMS value is suitable for capturing long-term changes in vibration behavior. For this purpose, the unfiltered time signals output by the F99 would be too frequent. The vibration sensors of the VIM series can therefore be used to determine whether the vibration behavior at a specific component in a machine changes over days, weeks, months or years due to wear and friction. From this, it can be deduced at an early stage whether the component in question needs to be serviced – before a critical failure occurs.
Vibration and acceleration sensors in wind turbines
If both short-term and long-term vibration changes are to be monitored, it is worthwhile to use a combination of vibration and acceleration sensors. This is the case in wind turbines, for example: The F99 monitors the vibration of the nacelle, while the VIM keeps an eye on the condition of rotating components inside the nacelle, such as the generator or the shaft-hub connection.
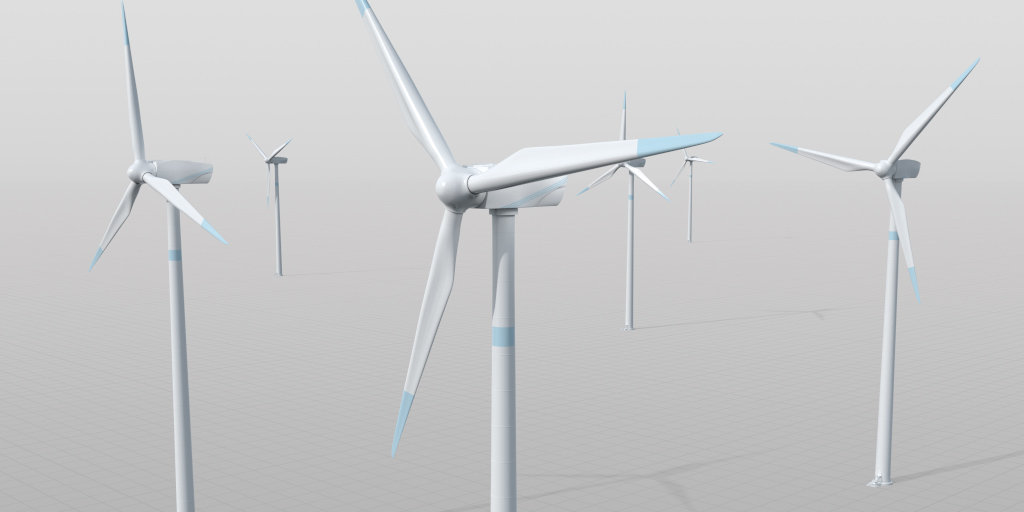
Control of the turbine with the acceleration sensor F99
In wind turbines, the rotation of the hub for power generation leads to an oscillation behavior (tilting back and forth) of the entire nacelle. The rotation speed of the hub determines the oscillation behavior of the nacelle. The F99 acceleration sensor is now mounted in the nacelle of the wind turbine. If the rotation of the hub becomes too strong, the vibration acceleration of the entire nacelle also increases. Since the F99 outputs individual instantaneous values at short intervals, the sensor immediately detects this change in vibration and gives the signal in time to control the hub speed accordingly.
Condition monitoring with the VIM vibration sensor
In contrast to the F99 acceleration sensor, the VIM vibration sensor is installed inside the wind turbine to monitor the quality of individual components over a longer period of time. Regardless of whether they are gears, generators or gear wheels, all rotating components suffer age-related damage over time due to misalignment or friction effects, therefore changing their vibration behavior. Without sensor measurements, the entire plant would have to undergo cost-intensive maintenance at increasingly shorter intervals, even if the function is not yet impaired. Since the vibration sensor detects long-term changes in vibration velocity or acceleration, it enables condition monitoring as well as predictive and targeted maintenance of the components concerned. This means that maintenance only needs to be performed when it is actually required. The vibration sensors from Pepperl+Fuchs guarantee a high level of safety in the process through corresponding certifications – up to SIL 2/PL d for the VIM8 series.
Subscribe to our newsletter and receive regular news and interesting facts from the world of automation.