5 Ways to Use K-System Interface Technology in Wastewater Treatment Plants
Content of This Article
5 Ways to Use K-System Interface Technology in Wastewater Treatment Plants
Large-scale industries like manufacturing and mining produce millions of gallons of wastewater every day. This wastewater can be reused or returned to the environment after going through a wastewater treatment plant. The average time it takes to successfully treat water once it enters the plant is heavily influenced by the technology available. While treatment can take less than a day in some plants, it can take up to 36 hours in others. But if a plant is equipped with the latest process automation technology, wastewater treatment takes less time.
The K-System portfolio from Pepperl+Fuchs can be used to streamline processes at wastewater treatment plants. K-System interface technology comes in every signal variation, ranging from simple isolators to highly functional modules. The components are DIN rail mountable and can be powered via Pepperl+Fuchs’ power rail and power feed module. The power feed module is even capable of sending line faults to the customer’s control system via collective error messaging from the power rail.
In this blog article we show five ways the K-System portfolio can be used in wastewater treatment plants.
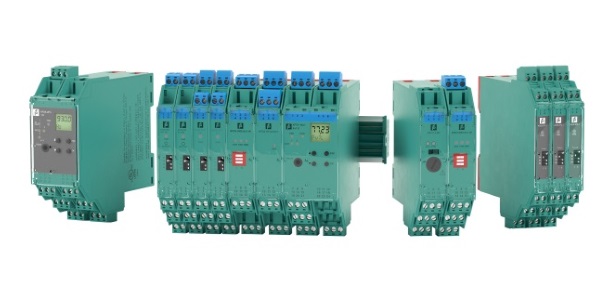
K-System Interface Technology from Pepperl+Fuchs
1. Monitoring Inflow Pumps
Inflow pumps carry wastewater from its initial source to the treatment plant. Solid objects present in incoming wastewater can block these inflow pumps, causing damage and expensive downtime if not caught early. K-System frequency converters monitor the rotational speed of each pump by reading out discrete sensor signals. Monitoring is constant, so problems can be quickly identified and resolved if pump blockage does occur.
2. Preventing Overflow
Wastewater treatment plants can use rainwater stored in retention basins to control water flow rate. However, the basins themselves must never overflow. Plants can use ultrasonic level transmitters to detect fill level inside the basin, and K-System transmitter power supplies can be used to transmit sensor readings to the control room.
It is essential that the sensor signals always reach the control room so the plant operator knows when to engage the rainwater pumps. These pumps, like the inflow pumps, can be equipped with K-System frequency converters to monitor rotational speed. This allows operating personnel to switch to backup pumps if the frequency converters detect a broken pipe or other issues that require reserve pump activation.
3. Ensuring Proper Biological Breakdown
Wastewater can contain high salt loads, lyes, and acids. In large amounts, these agents can interfere with the decay of organic material. This is why the control room must monitor the water’s conductivity and pH values. K-System transmitter power supplies with adjustable limit values can be used to reliably transmit these measured values to the control room.
4. Enhancing Water Clarification
After wastewater makes its way through the bar screen for large object removal, it heads to the sand trap—the second stage of the mechanical cleaning process for fine particle and oil/fat removal. In this stage, water can be cleaned using an unventilated or ventilated sand trap. In an unventilated sand trap, sand and other particles collect as the flow speed of the wastewater is reduced, and can then be siphoned off the bottom. Flammable oil and fat remain in the basin. In a ventilated sand trap, air is blown into the basin from below, causing matter to sink and collect on the bottom. Sand pumps mounted on a mobile scraper bridge are used to siphon the sediment particles from the drain or from a funnel on the bottom of the sand trap. By contrast, oil and fat are deposited on the surface and are removed by an oscillating surface scraper equipped with a suction device.
The position of the skimmer is determined and reported on using discrete sensors operating in conjunction with switch amplifiers. Sensors and frequency converters monitor the rotational speed of the sand pumps. The level measurement for the deposited sand is transmitted to the control panel using a transmitter power supply and a level transmitter. Depending on whether the plant has Ex-rated hazardous conditions, the modules are available as intrinsic safety barriers from the K-System product family or as general-purpose signal conditioners from the K- and SC-Systems families.
5. Generating Energy
After the wastewater has made its way through the primary clarifiers, the sludge produced from these stages travels to a digestion tower for decomposition. The 25-day, airtight decomposition process breaks down the sludge, producing gas, water, and sapropel. The 70% methane, 30% carbon dioxide gas mixture is then cleaned and the remaining gas is either burned off or stored for energy generation.
Since digestion towers and their secondary systems are essentially hazardous areas, K-System intrinsic safety barriers can be used as interface modules. Transmitter power supplies report the level and pressure measurements from the digestion tower to the control panel while temperature converters report analog temperature values.
In conjunction with sensors, K-System frequency converters record and transfer motor data from the digestion tower’s agitator to stop pipe blockages and prevent foam from flooding the plant. Gas analyzers transfer their results to the control panel via signal converters to reliably measure gas quality. The fill level and pressure measurements in the gas storage tank are transmitted in the same manner to prevent hazardous gas from escaping into the plant.
Subscribe to our newsletter and receive regular news and interesting facts from the world of automation.