Hardware and Software Features of the R2000 Series 2-D Laser Scanner
Content of This Article
Hardware and Software Features of the R2000 Series 2-D Laser Scanner
Whether used in warehouses, robotics, or dynamic applications for navigation of automated guided vehicles (AGV)―the 2-D LiDAR sensors of the R2000 series feature a gapless all-around visibility of 360°. The sophisticated laser scanners come with the innovative Pulse Ranging Technology (PRT) that helps providing reliable and extremely precise measuring results. In this blog post we’ll take a closer look at the hardware and software features of the R2000 2-D Laser Scanner and how these can help solve your individual application.
Software Features
Scan Data Filter
The scan data filtering function adds an option for pre-processing in the R2000, reducing the amount of scan data output while still utilizing the high scan resolution and providing higher performance in the output data.
Scan data filtering combines a configurable number of N adjacent scan points (window size) into a single scan point (block-wise processing) using one of various predefined algorithms. A filter algorithm calculates both a distance value and an amplitude value from the input data. The resulting scan point is placed at the center of the processing window for both angular value and timestamp value. All operations are performed in the sensor coordinate system.
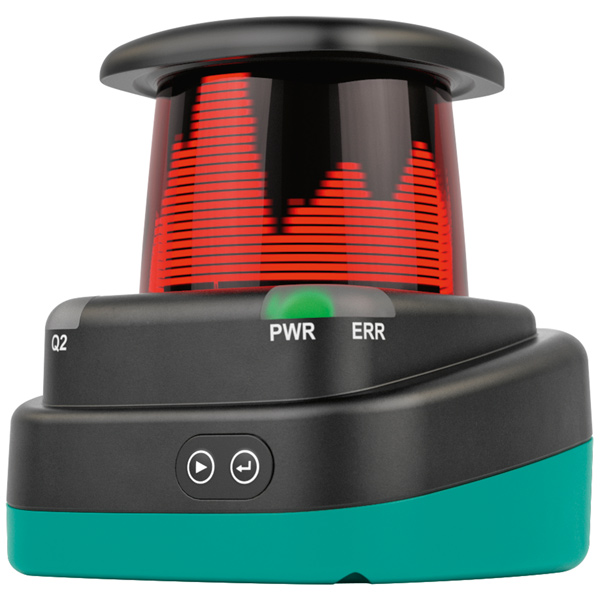
R2000 2-D laser scanner for precise measurement and navigation tasks
Users can choose from four different filters for pre-processing, including an average/median filter, maximum filter and a remission filter. The average/median filters are used to minimize noise level and to achieve higher measurement precision. The maximum filter helps reduce disturbed measurements by dust or very small objects such as raindrops in the near field to ensure reliable operation outdoors and in harsh environments. The remission filter helps suppress low reflective targets by separating measurements on reflectors and natural targets in the scanner itself.
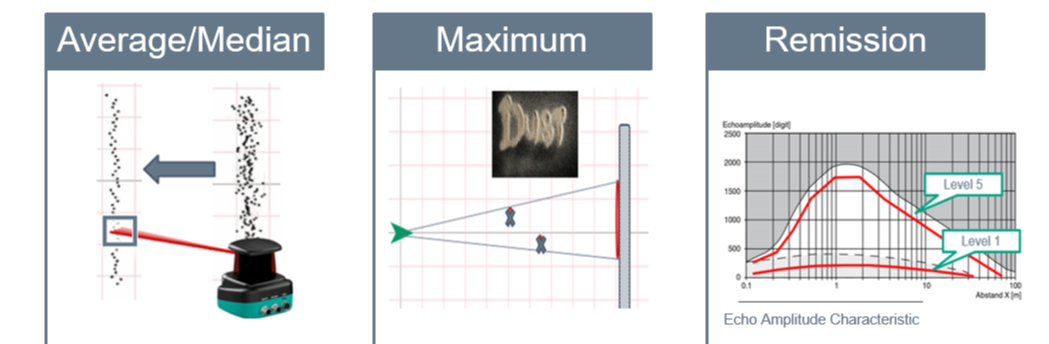
Skip Scan Function
The Skip Scan function allows to reduce the output frequency of scans over a scan data connection in comparison to the recording frequency of scans as defined by the global parameter scan frequency so that only, e.g., every second scan is transferred and the output of the next is suppressed. This option is useful for applications that require a high scan frequency in order to reduce the motion blur effect of recording scan data in a dynamic environment (AGV for instance), but do not require all scan data at high frequency.
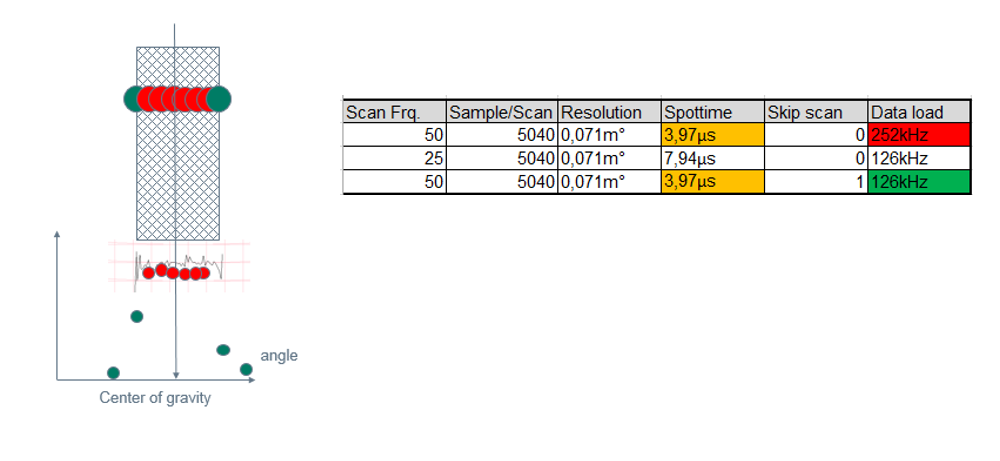
Hardware Features
Hardware Timestamp
The hardware timestamp provides a highly precise synchronization of the sensor’s raw system time with the system time of an external client. This eliminates latency time and jitter of the software synchronization via Ethernet, leading to a synchronization accuracy of less than 1 ms. It also improves position accuracy during navigation of automated guided vehicles.
I/O Access
This features enables the command access to two I/Q channels that can be used as either digital input or digital output. This allows for easy support of peripheral hardware close to the scanner or advantages for client controllers with limited I/Q’s.
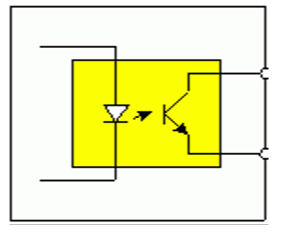
Lens Contamination Monitor
The Lens Contamination Monitor (LCM) continuously monitors the transparency or contamination of the scanner lens. If the transparency drops below a predefined level, the scanner provides a warning to clean the lens before range reduction takes effect. The warning level can be set to three different levels―low, medium, and high sensitivity. As the lens is divided into twelve sectors at 30°, the LCM for each sector can be activated independently.
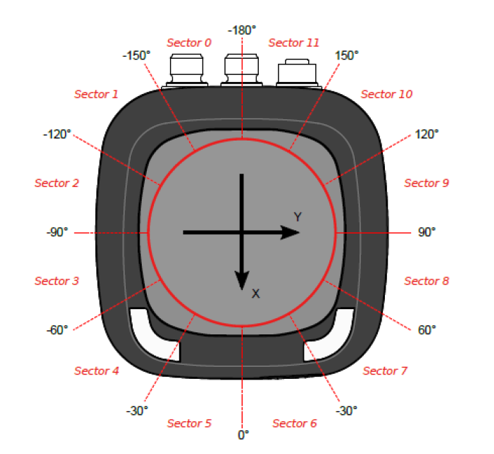
Division of the scanner lens into twelve sectors of 30°
More Information
Watch on YouTube: How do I configure the monitoring fields of the laser scanner R2000 Detection?
Subscribe to our newsletter and receive regular news and interesting facts from the world of automation.