Reliable Level Measurement—Why Two Different Technologies Are Crucial
Content of This Article
Reliable Level Measurement—Why Two Different Technologies Are Crucial
Level measurement technology is the basis for reliable process control in the chemical, petrochemical, environmental, and other related industries. In order to ensure an efficient and trouble-free process flow, limit levels in tanks, silos, or containers must be reliably monitored. Level measurements also provide precise data on consumption. Reliable and robust level measurement technology is essential, especially for critical applications and in potentially explosive areas. Find out in this blog article why it is advisable to use a different principle of measurement for the probe and technology for continuous level measurement and level limit detection in critical tank level applications.
What Are the Two Types of Level Measurement?
There are two types of level measurement and level control:
Point level detection – also known as level limit detection
A level limit switch or point level is usually a probe that only provides a discrete output signal when the level reaches the probe or responds to it. It only signals to the operating personnel that a certain level has been reached, but does not indicate the height of the level. Level limit switches protect the pumps from overflowing or running dry.
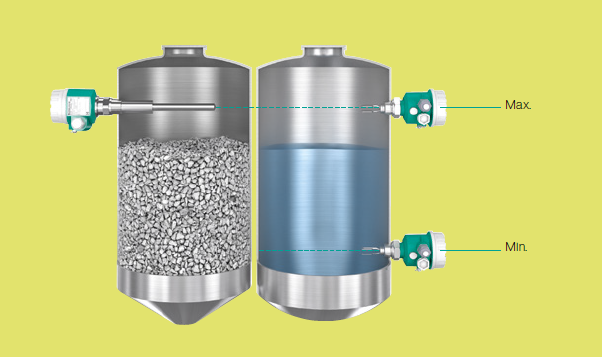
Level limit measurement for solid and liquid goods
Continuous level measurement
With continuous level measurement, the measuring probe indicates the exact height of the fluctuating level in the tank. Devices for continuous level measurement can be set so that the level in the tank is always indicated. Switch points for low-low or high-high level can be added as alarm points. This setting indicates to the operator that the level has reached a critical height.
The continuous measuring probe can be set up for both continuous level measurement and point level monitoring. Although this setting is convenient, it can lead to problems if the probe and/or the technology used provide incorrect measurements due to insufficient feedback, for example, due to an extended foam layer.
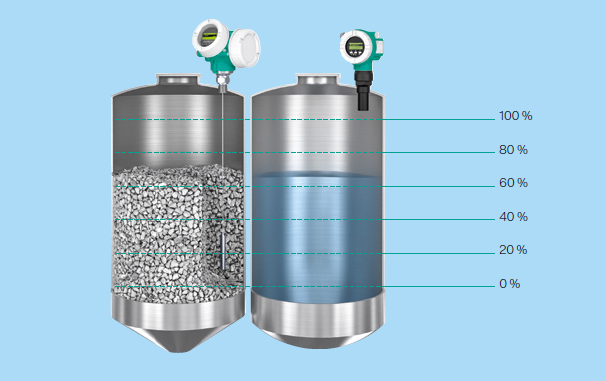
Continuous level measurement for solids and liquids
Why Should I Use Two Different Level Measurement Techniques to Prevent Critical Tank Levels?
In most tank level applications, it is good engineering practice to add a high-high and/or low-low level alarm to indicate an abnormal tank level. In critical tank level applications, it is not advisable to use the same probe and/or technology for both continuous level measurement and level limit detection. If the continuous probe or the probe technology fails, i.e., the medium no longer responds to the probe, the operator loses both the continuous measurement values and the feedback from the level limit detection.
If the level probe fails, the operation does not know the fill level of the tank or perceives it as low and continues to run the pump. Without a high-high alarm, an overflow condition can simply occur due to the failure of the probe. If the fill level is too low, there is a risk of dry running and serious process interruptions.
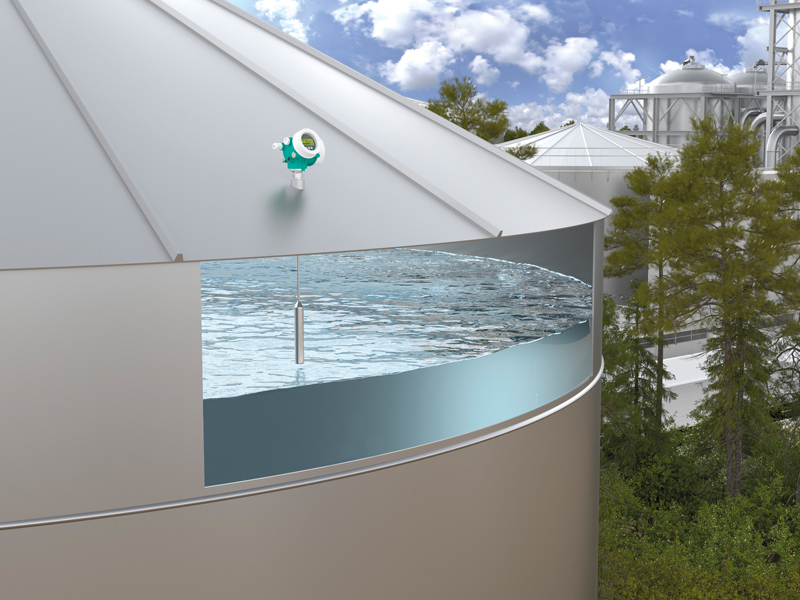
Why Are Two Different Technologies Crucial for Level Measurement?
When selecting a device, the technology of the probe is often not sufficiently considered and two probes of the same principle of measurement can be used for redundancy. For example, if we use an ultrasonic sensor for continuous level measurement of liquids, but there is too much foam on the top layer, the sensor may provide insufficient or incorrect feedback. If the redundant alarm point probe is of the same technology, it can also provide incorrect values due to the foam layer. Not only can the probe fail, but the technology used for detection could also fail in certain applications. It is therefore crucial to use two different technologies for level measurement.
What Is a Cost-Effective, Redundant Solution for Level Limit Detection in Liquids?
The LFL series float switches from Pepperl+Fuchs offer an alarm output and represent a different technology to level limit switches, probes, or other level sensors. This makes them a cost-effective, easy-to-install, redundant solution for level limit detection in liquids. All Pepperl+Fuchs float switches, such as the LFL2 series, are mercury-free and available in a variety of cable materials and lengths. They are suitable for the most common applications for level measurement in tanks and for most corrosive liquids. Ball and float versions are available depending on the density of the material.
The LFL float switches have a contact, PNP, and NAMUR output for hazardous areas. In combination with an intrinsic safety barrier, such as the KCD2-SR-EX2* switch amplifier from Pepperl+Fuchs, they are a safe solution for point level detection in hazardous areas. An LFL float switch can also be set up to trigger a high-level alarm if another technology fails internally or if there is too much foam on the surface.
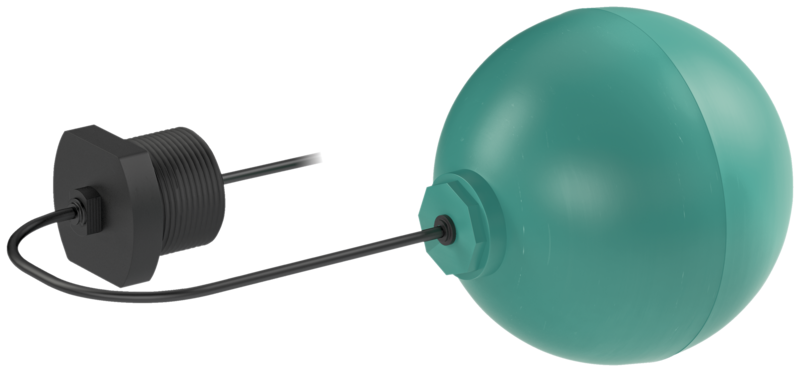
LFL series float switch for level limit detection in liquids
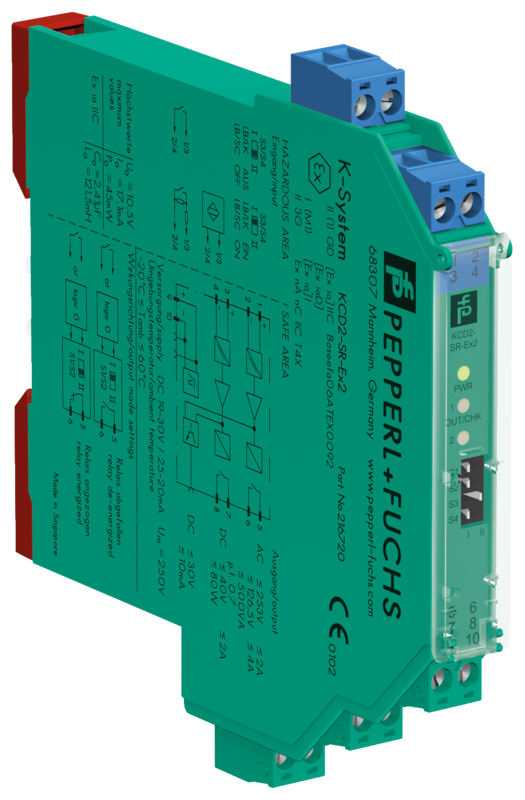
Combined with an intrinsic safety barrier, such as the KCD2-SR-EX2, it is a safe solution for point level detection in hazardous areas.
More Information
Subscribe to our newsletter and receive regular news and interesting facts from the world of automation.