Three Functions in a Single Sensor: Overview of Radar Sensor Measuring Modes
Content of This Article
Three Functions in a Single Sensor: Overview of Radar Sensor Measuring Modes
Advanced FMCW (frequency-modulated continuous-wave) radar sensors from Pepperl+Fuchs integrate an unprecedented range of functions in an extremely compact design. These sensors are designed around a physical sensing principle that allows for both diversity and ruggedness. Electromagnetic waves emitted by the sensor propagate in the environment until an object is encountered, which results in the initially emitted electromagnetic waves being reflected. Depending on the material, shape, size, direction, or speed of the object, these radar reflections possess different properties, which allow the downstream evaluation electronics to draw conclusions about the nature of the detected object.
Therefore, these devices are able to very precisely determine the distance, direction of movement, and speed of objects in the sensing range. For this purpose, three different measuring modes are integrated into a single sensor type. Here is an overview of these three modes and how you can use them effectively in different application scenarios.
Measuring Mode “First Object”
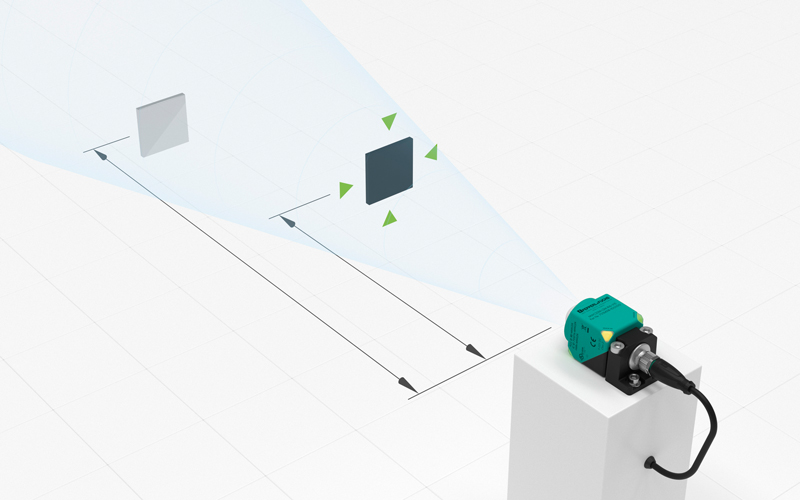
Illustration: Two potential targets are in the sensing range of the radar sensor. Although the metal plate has much better reflection properties than the plastic plate, the sensor still detects the plastic plate as the primary target.
Explanation: In “first object” mode, the object closest to the radar sensor is detected regardless of the material. This means that, contrary to assumptions, a metal, highly reflective object in the sensing range of the sensor does not automatically interfere with, or even exclude, the detection of less reflective objects. This measuring mode is based on a change in the frequency of the electromagnetic wave when it hits a target object, which can be explained by the Doppler effect. Due to the shorter distance and elapsed time, the signal reflected back by the first object in the sensing area of the sensor (radar reflection) has a stronger “compression” than the signal from the object further away in the background. This allows the sensor to detect this object as the first object in the sensing range.
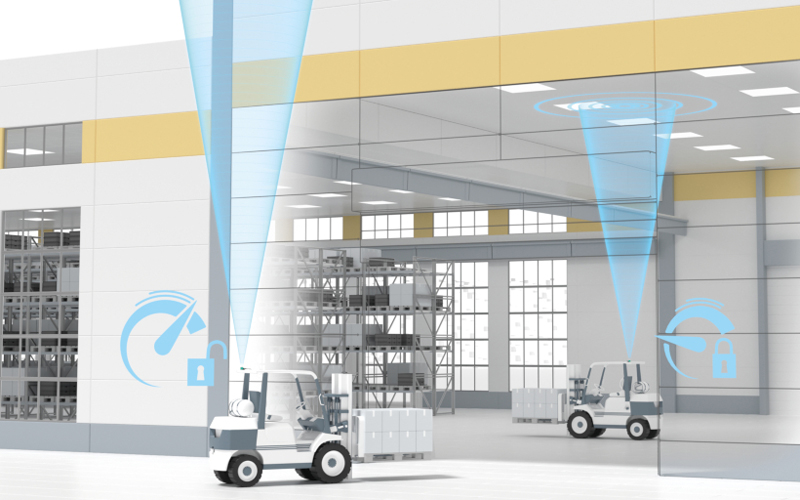
Application Example: Speed is a decisive factor in material handling. This also applies to the use of forklifts on company premises. If high speeds dare still an advantage in outdoor areas, where the surroundings are usually easy to see, some amount of restriction is still necessary inside factories and warehouses for safety reasons. To better protect personnel from this concern, a vertically aligned radar sensor—which detects the “first object” as the hall ceiling or the metal cross struts below it—can immediately determine when the forklift has reached an indoor area. At that time, the maximum possible speed is automatically limited to a tolerable level and only released again when leaving the hall. To avoid an unwanted limitation of speed under crossbeams or bridges in the open field, which the sensor will also register as the “first object,” high filter strength and low sampling rate settings can be applied.
Measuring Mode “Best Reflection”
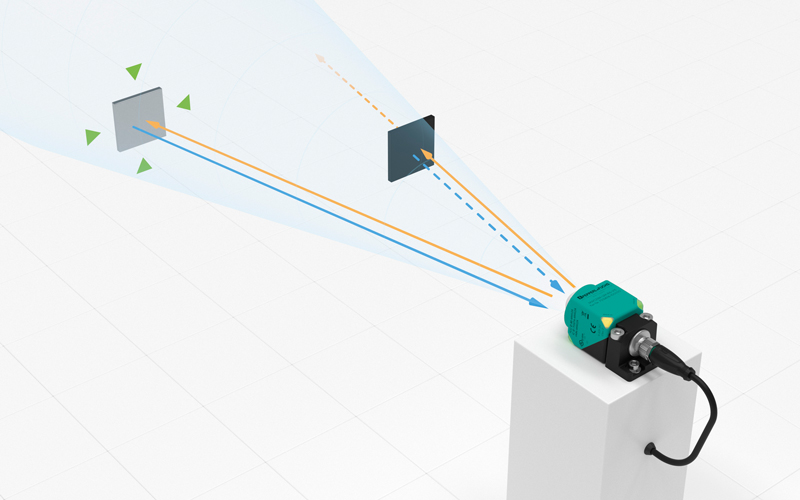
Illustration: Two potential targets are in the sensing range of the radar sensor. Although the plastic plate is closer to the sensor, the sensor still detects the metal plate in the background as the primary target.
Explanation: Due to their small wavelength (2.45 mm at 122 GHz), the microwaves emitted by the radar sensor behave similarly to light, meaning that effects such as diffraction, total reflection, deflection, interference, and some others occur. In the example shown, the electromagnetic waves mostly penetrate the plastic plate and are only partially reflected, whereas they are completely reflected by the metal plate. The amplitude strength of the radar reflection from the metal plate is therefore significantly higher than the reflection formed by the highly permeable plastic plate.
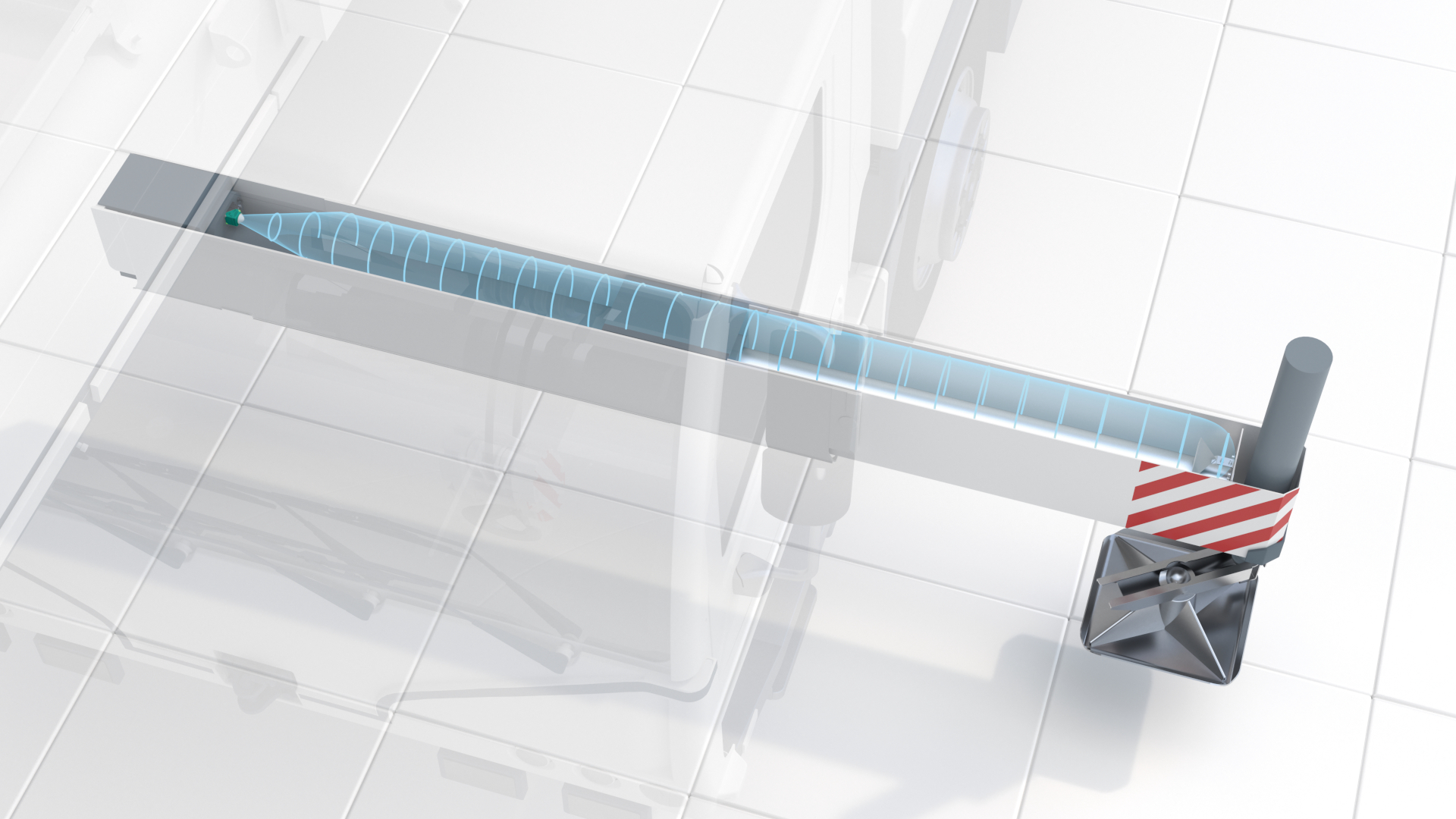
Application Example: “Best reflection” mode has a number of uses. For example, by installing metal corner reflectors, the detectability of otherwise weakly reflective objects can be greatly increased. An example of this is the precise control of mobile crane outriggers. The radar beam of a radar sensor mounted inside the telescopic crossbeam is directed at a corner reflector positioned at the tip. If the telescopic crossbeam moves forwards or backwards when the outrigger is extended or retracted, the sensor measures this change in distance and transmits the values to the crane’s control system as a basis for further adjustment processes. Dirt deposits and residue from hydraulic oils—which make measuring difficult—can be reliably hidden in the “best reflection” measuring mode, with orientation toward the corner reflector.
Another example application for this operating mode is the measuring of the fill level in closed containers, without having to drill or cut a hole in the outer layer. The basic prerequisites here are that the medium to be measured has a high reflectivity and that the material properties of the tank, or the point through which the sensor measures, allow effective transmission of the radar wave.
Measuring Mode “Fastest Object”
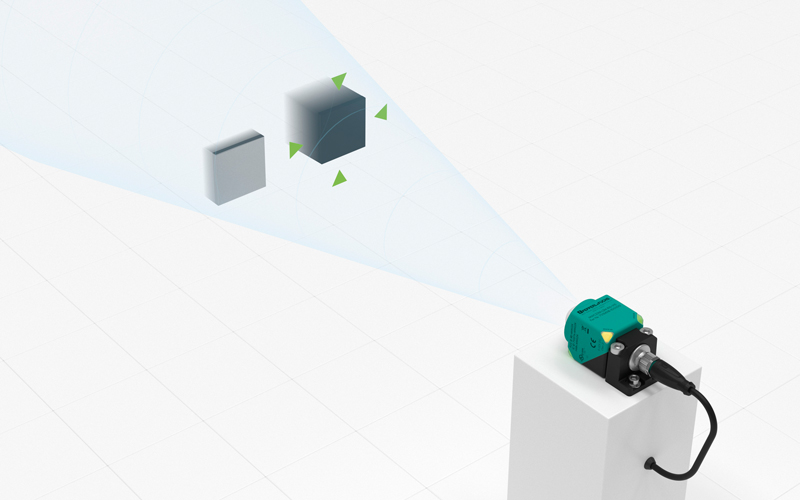
Illustration: Two potential targets move at different speeds toward or away from the sensor. The radar sensor detects the radial speed of both targets and recognizes the faster object as the primary target.
Explanation: Due to the FMCW modulation process used by radar sensors from Pepperl+Fuchs, the relative speed of a detected object is also available as process data via a measurement of the Doppler shift in each measuring cycle. The term “relative speed” refers to the fact that these measurements do not detect the actual real speed of an object: Instead, the radial speed, i.e., the part of the motion that acts toward or away from the sensor, is measured. However, the method does not detect tangential speeds or speed components.

Application Example: The “fastest object” measuring mode is ideal for implementing advanced collision protection for AGVs. If several objects are moving toward the vehicle in the periphery of an AGV, for example, the greatest risk of collision does not necessarily arise from the objects closest to the vehicle, but from the object moving toward the AGV at the fastest speed. In the “fastest object” measuring mode, the radar sensor detects the speed and distance of this object, which can be used to calculate when a collision will theoretically occur and whether slower travel should be initiated depending on current rates of speed.
Furthermore, this measuring mode offers the capability to perform reliable speed measurements, even if highly reflective and therefore potentially interfering static objects are in the sensing range. These objects can be easily hidden during the measuring process in the “fastest object” mode.
Radar Sensors—Defying the Elements
The following video provides a brief summary of the three different measuring modes of radar sensors.
More Information
Subscribe to our newsletter and receive regular news and interesting facts from the world of automation.