Sensors and Systems for Conveyor Belts in the Mining Industry
Content of This Article
Sensors and Systems for Conveyor Belts in the Mining Industry
The mining industry requires various methods to transport bulk materials of varying volumes over long distances. For example, conveyor belts provide an efficient and cost-effective method of material transportation. To ensure optimum performance and maximum efficiency over the lifetime of the conveyor belt, the automation equipment used to control and monitor must be of the highest quality. Numerous robust sensors from Pepperl+Fuchs offer solutions for economical, efficient, and reliable operation of conveyor systems in the mining industry.
Ultrasonic Sensors to Measure the Cake Thickness Level
In mining, measuring the cake thickness level refers to the continuous monitoring and control of the height of the wet ore layer, called the “cake”, on the conveyor belt. Here, eight ultrasonic sensors (such as UC500-18GS or UC500-30GM) with an IO-Link interface are mounted in a row above the belt in a system called “Cake Thickness Profiler” along with the IO-Link Master ICE2 and used for reliable ore profile generation. Sound waves are emitted towards the conveyor belt, and the time it takes for the waves to be reflected back is measured. The profile of the ore on the conveyor is generated based on the distance measured by each sensor. This solution is an alternative to laser scanner solutions which are often affected by the dusty environment seen in mining.

UC500-18GS series ultrasonic sensor from Pepperl+Fuchs
Ultrasonic Sensors to Detect Belt Rips and Tears
For the detection of conveyor belt rips, ultrasonic sensors such as the UC500-30GM-IUEP-IO-V15 are a proven solution. The sensors monitor the integrity of the belt by detecting anomalies that indicate tears or rips. Eight sensors are mounted in a row underneath the conveyor belt and emit high-frequency sound waves towards the belt and measure the reflected waves. This measurement provides a large sampling area. When the conveyor belt is intact, the sound waves are consistently reflected back to the sensor. If there is a rip or tear, the reflected wave pattern is disrupted. The sensor continuously and reliably scans the belt surface as it moves and any significant deviation from the reflected wave pattern triggers an alert. The sensors can be synchronized when mounted next to each other, which prevents sensor crosstalk and allows the minimum separation distance to be reduced.
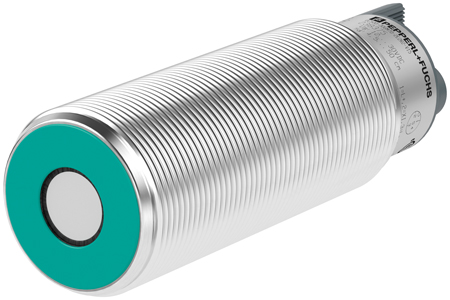
UC500-30GM series ultrasonic sensor from Pepperl+Fuchs
Inductive Sensors to Ensure Belt Alignment and Prevent Run-Off
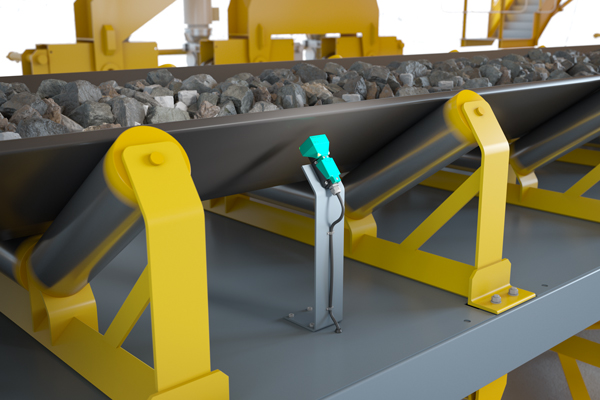
In conveyor systems, ensuring the proper alignment and preventing belt run-off is crucial for maintaining smooth operations and avoiding costly downtime. Pepperl+Fuchs offers a reliable solution with the VariKont inductive sensor NBN40-U1L-Z2. The highly resilient sensors can withstand challenging industrial environments, provide long-lasting performance, and offer several benefits such as high switching distances of up to 50 mm, a rotatable sensor head, and a dual LED indicator for 360˚ visibility. Positioned on each side along the conveyor belt to detect any misalignment or deviations in the belt path, the sensors detect the presence of metal rebar reinforcements within the belt. If the belt drifts to one side or becomes misaligned, the sensor will not detect the rebar and switch “off,” indicating a belt misalignment. This immediate feedback allows for timely corrective actions, preventing potential run-off, and ensuring continuous operation.
Inductive Sensor and Rotation Speed Monitor to Detect Belt Underspeed
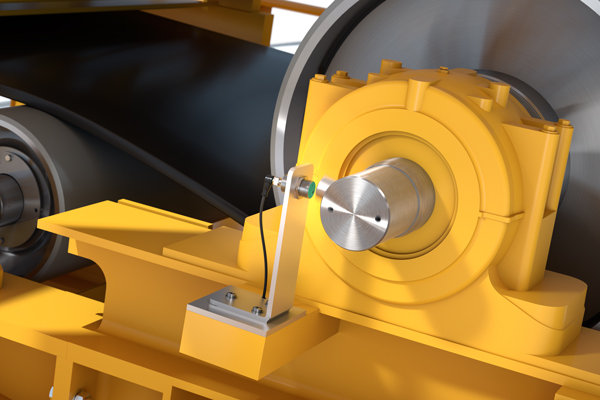
The speed of a conveyor belt can be monitored using a rotation speed monitor (KFU8-DW-1.D) with analog output and alarm outputs in combination with a magnetic sensor such as an inductive sensor (NBN40-U1L-Z2 or M18/M30 series). Mounted underneath the conveyor belt, the sensor monitors the passage of metal bolts attached to the belt. As the belt moves, the sensor detects rotational movements, generating pulses or signals proportional to the rotational speed. These signals are sent to a monitoring unit, which calculates the belt’s speed (up to 40 kHz) based on the frequency of the pulses. This information is then used to trigger an alarm if the speed deviates from the set speed, ensuring the belt operates within the desired speed range for optimal performance and safety.
Simultaneously, the rotation speed monitor receives pulses from the sensor, each pulse indicating a rotational position. By calculating the time interval between the pulses, the belt’s speed is determined. If the speed falls below a set threshold (underspeed), the rotation speed monitor triggers an alarm. Underspeed sensing is important for a conveyor belt as it detects slowdowns or stoppages, which can indicate mechanical failures or material jams.
Subscribe to our newsletter and receive regular news and interesting facts from the world of automation.