PROFINET Gateways for Remote I/O Systems—Spotlight on Four PROFINET Functions
Content of This Article
- S2 System Redundancy—Communication Using Redundant Controllers Ensures Process Reliability
- Ring Redundancy—High Availability through Path Diversity
- Shared Device Function Reduces the Number of Devices in the Field
- Dynamic Reconfiguration Enables Changes during Operation
- PROFINET Gateways for Remote I/O Systems from Pepperl+Fuchs
- More Information
PROFINET Gateways for Remote I/O Systems—Spotlight on Four PROFINET Functions
The PROFINET industrial Ethernet protocol offers various standardized functions for process automation that ensure high plant availability. These functions affect the infrastructure, the field devices, and the control system. Standardization ensures a high level of interoperability. The flexible network topology, intelligent diagnostic concepts, and fast data transfer of PROFINET technology ensure high efficiency from engineering to maintenance. PROFINET makes your installed device base and control technology compatible with IIoT applications. The PROFINET gateways for the LB and FB remote I/O systems from Pepperl+Fuchs offer four relevant PROFINET functions for plants that require high availability. Learn more about the benefits of PROFINET for remote I/O systems in this blog article.
S2 System Redundancy—Communication Using Redundant Controllers Ensures Process Reliability
S2 system redundancy refers to communication between a device and two controllers that use a redundant configuration. In this configuration, the controllers each establish their own logical connection to the device. This connection is called an application relationship (AR). A controller is randomly assigned the active role. When a switch is required, the controller can seamlessly take control because of the AR already established between the passive controller and the field device—typically in less than 200 milliseconds.
In this context, the PROFINET gateway for the LB or FB remote I/O systems from Pepperl+Fuchs assumes the role of a field device and maps all connected sensors and actuators in the controller. This means that process control continues to function even in the rare event of a control failure, and redundancy switching prevents unwanted plant shutdowns.
Ring Redundancy—High Availability through Path Diversity
The network can be configured in a ring topology so that each node in the ring can communicate with every other node via two channels. PROFINET networks use the standardized media redundancy protocol (MRP), which must be supported by all devices acting as ring nodes. This topology is actually not permitted, since the Ethernet protocol would send messages around the ring and immediately overload the network. For this reason, one point in the ring contains only one logical opening. A ring manager checks the communication with all nodes at regular intervals. If there is a disruption in the ring, the ring manager—also known as the ring master—closes the opening in the logic and redirects traffic to the nodes that are not normally connected. Practical tests have shown that redundancy switching can be achieved in less than 200 milliseconds. In the engineering phase, the planner determines which controller, switch, or device should assume the role of ring master.
The PROFINET gateways for the LB and FB remote I/O systems support MRP and each have the required two ports. The integrated switch is very cost-effective, as no additional hardware is required in the hazardous area. They can therefore be easily integrated into any ring topology.
Shared Device Function Reduces the Number of Devices in the Field
PROFINET enables a sensor to send its measured data to several controllers. To do this, the controllers “subscribe” to the required measured values when establishing the AR with the field device, and the device “publishes” the measured values to all registered controllers without being prompted. This concept is called the Publisher/Subscriber pattern or Pub/Sub for short.
A similar concept exists for actuators: several controllers can trigger actuating or switching operations via a gateway, with each actuator being specifically assigned to a controller.
In other words, the remote I/O is a shared device for multiple controllers and systems. On an LB or FB remote I/O station, up to 184 inputs or outputs can be configured and assigned to any controller during engineering. This prevents measured values from being recorded twice, for example, which can occur during transfers or differential measurements. It allows users to reduce the number of devices and control cabinets, as well as the effort required for piping and wiring.
Dynamic Reconfiguration Enables Changes during Operation
Dynamic reconfiguration—also called dynamic configuration—refers to a procedure for adding or removing devices from an existing PROFINET system. It allows engineers to change the device settings dynamically—i.e., during operation—without having to put the controller into stop mode.
The PROFINET LB and FB remote I/O systems from Pepperl+Fuchs not only use dynamic reconfiguration to make changes to the field devices, but also extend the concept to the plug-in I/O modules—whose number and signal type can also be freely configured. This offers maximum flexibility and reduces the effort required, such as when changing products. In smaller plants, for example, only one remote I/O is needed to control several reactors. In these cases, one process can be reconfigured while neighboring processes continue to run without interruption. This allows users to operate their plants at maximum capacity.
PROFINET Gateways for Remote I/O Systems from Pepperl+Fuchs
The modular remote I/O systems connect sensors and actuators in hazardous areas to the control system or process control system. A PROFINET gateway enables connection to Ethernet networks and paves the way for IIoT applications. The PROFINET gateways for LB remote I/O systems (Zone 2, Class I/Div. 2) and FB remote I/O systems (Zone 1) from Pepperl+Fuchs offer all four of the aforementioned PROFINET functions for process automation, allowing full flexibility in terms of channel configuration and plant availability. They support HART/HART IP and enable the transmission of process variables and additional status information from field devices at high speed. Pepperl+Fuchs remote I/O systems are available in stainless steel or glass-fiber reinforced (GFRP) enclosures.
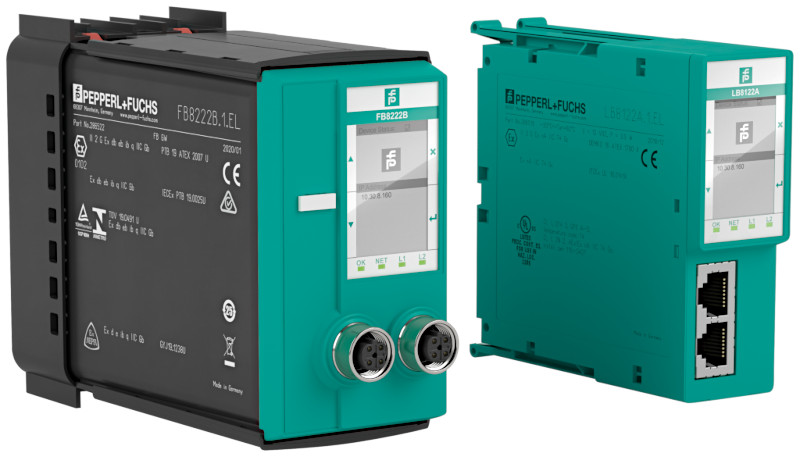
PROFINET Gateways for LB and FB Remote I/O Systems from Pepperl+Fuchs
More Information
- PROFINET-Gateway for LB remote I/O system (Zone 2, Class I/Div. 2)
- PROFINET-Gateway for FB remote I/O system (Zone 1)
Subscribe to our newsletter and receive regular news and interesting facts from the world of automation.